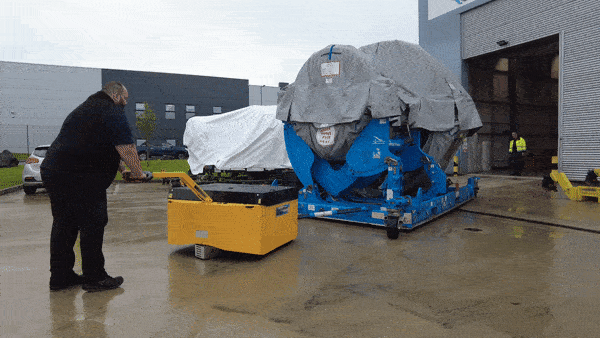
Blog
Welcome to the MasterMover blog, your hub for the latest expertise, industry insights, and essential resources to optimise material handling processes.
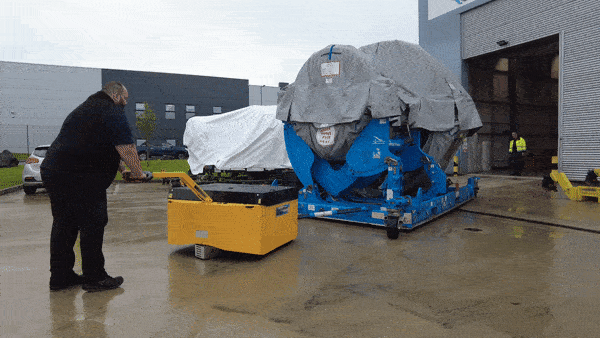
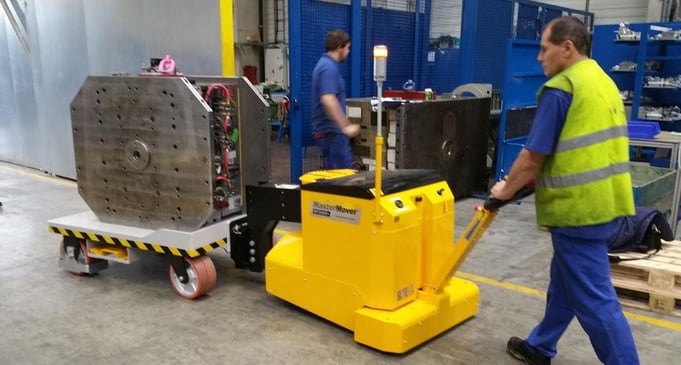
The Key to More Efficient Mold Changeovers
Mold changeovers cost money – so every second counts. Driving leaders across molding and manufacturing to reduce changeovers and increase efficiency.
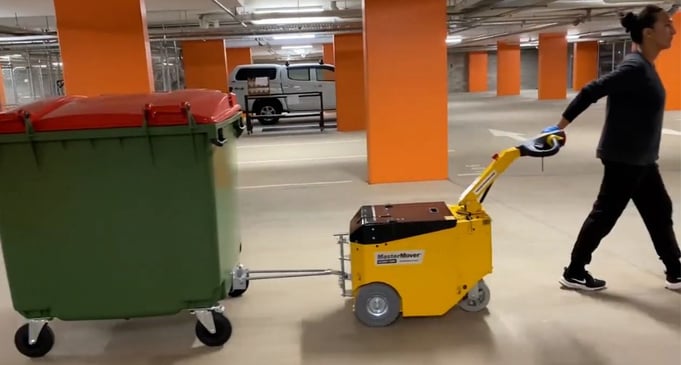
The Dangers of Moving Loaded Bins by Hand
The age-old adage, "Safety first," rings especially true in workplaces that involve the movement of heavy loads and equipment, ranging from automotive manufacturing to logistics. But, for many years, the manual movement of heavy bins has been an ...
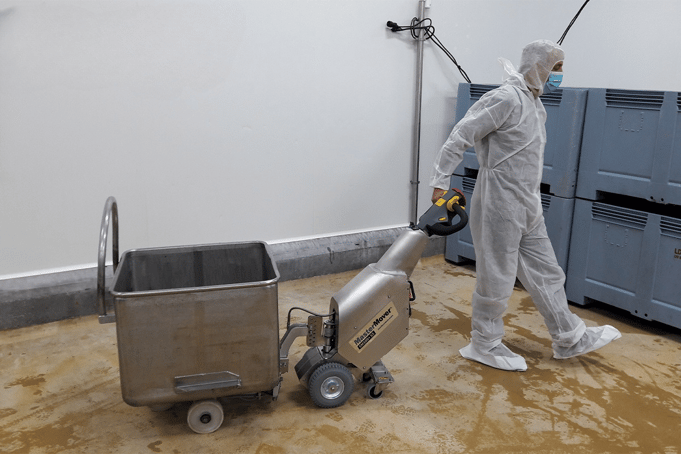
How to Move Food Eurobins Safely
What are Eurobins? Eurobins, also known as tote bins, containers or euro tubs, are a type of wheeled food handling container, often used for the transportation, storage, and handling of bulk food products or waste materials.
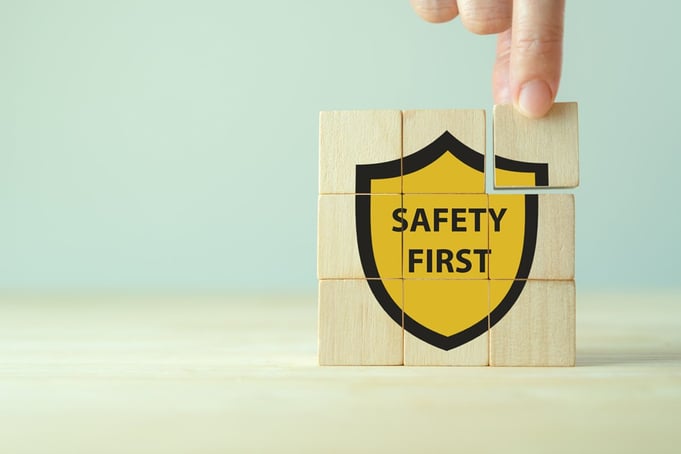
World Day for Safety and Health at Work
Every year, on April 28th, the world celebrates the World Day for Safety and Health at Work.
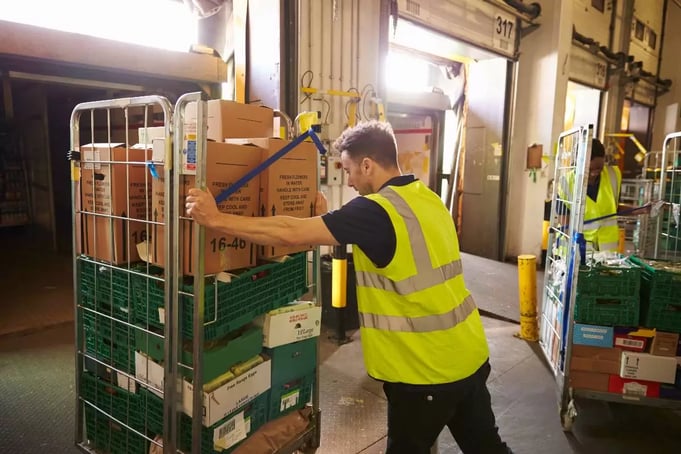
How To Move Supermarket Roll Cages Safely
Roll cages, also known as wheeled cages, warehouse cage trolleys, roll containers or retail cages – are used extensively in retail and warehousing operations.
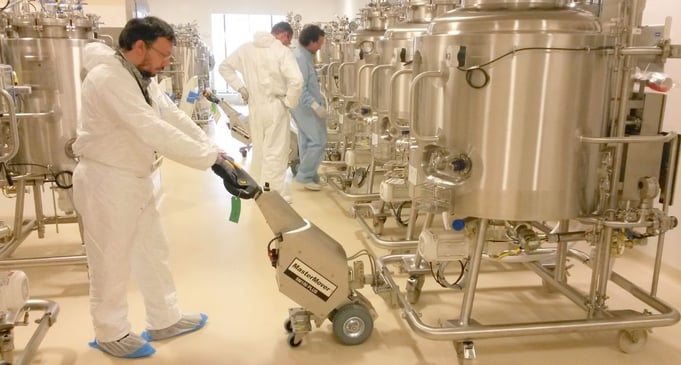
Looking East – Challenges & Opportunities in Asia’s Biopharma Industry
In 2020, the biopharma industry found itself on the lips of almost everyone – globally. The colossal effort behind the vaccine development transformed otherwise unknown manufacturers into household names overnight.
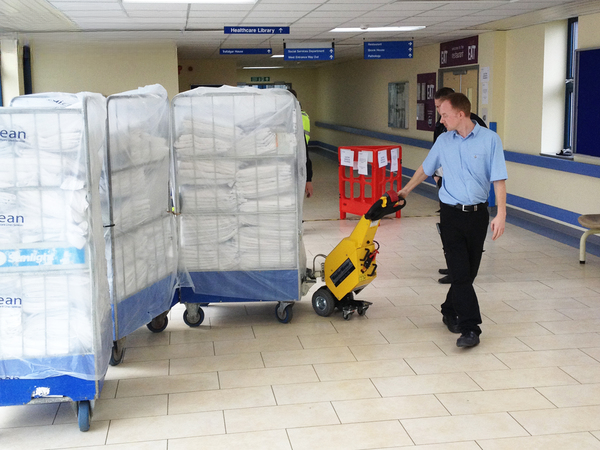
Health And Safety Executive Endorses Electric Tugs For Cost Saving In Hospitals
The benefits of electric tugs have been reinforced by the Health and Safety Executive (HSE) which has suggested that the use of them in hospitals provides an ideal solution for portering staff, allowing them to perform their vital role more ...
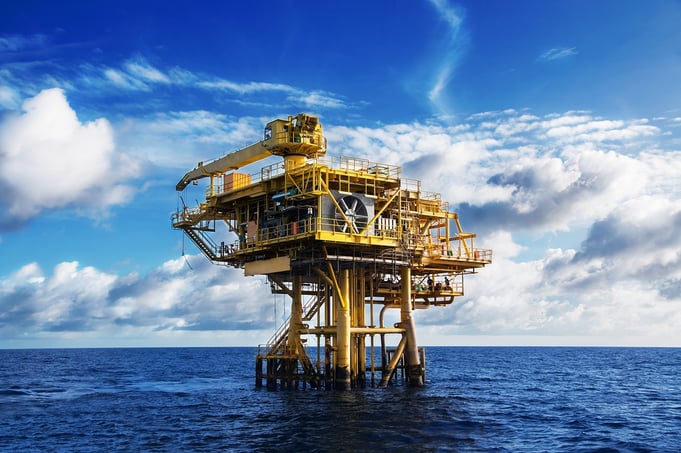
ATEX Electric Tugs Provide Safety and Efficiency North Sea
ATEX electric tugs engineered to the specific requirements of the UK oil and gas industry have been supplied by MasterMover.
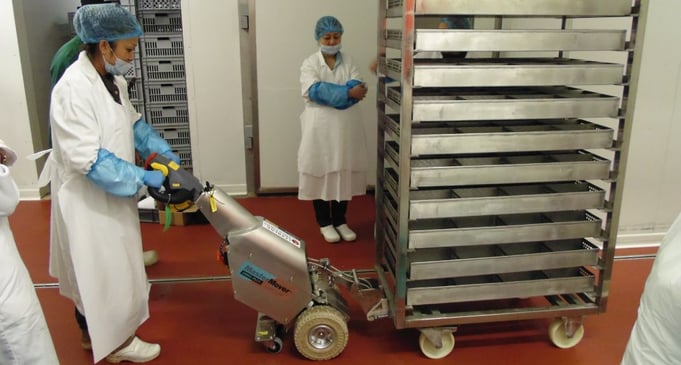
Labs and Kitchens Boost Safety With Stainless Steel Electric Tugs
When manufacturers want to adopt working practices that are agile, efficient and yet still meet the highest of safety standards, MasterMover’s stainless steel and ATEX compliant electric tugs are the obvious answer.
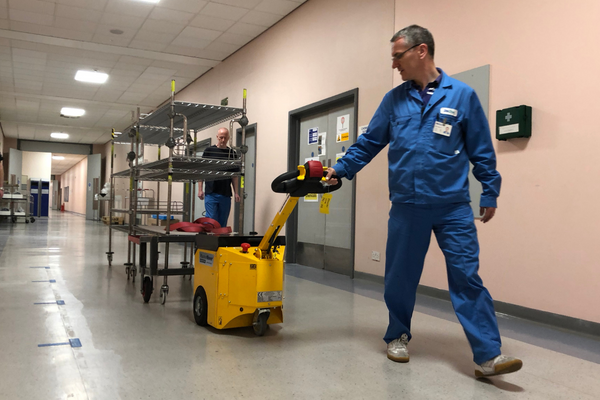
Improving Efficiency for Hospital Porters
For many, porters are the oil in the machine of many NHS hospitals, moving goods, equipment and patients around hospitals and proving a critical component in running clinical services smoothly. Here, Hugh Freer, European Director of electric tug ...
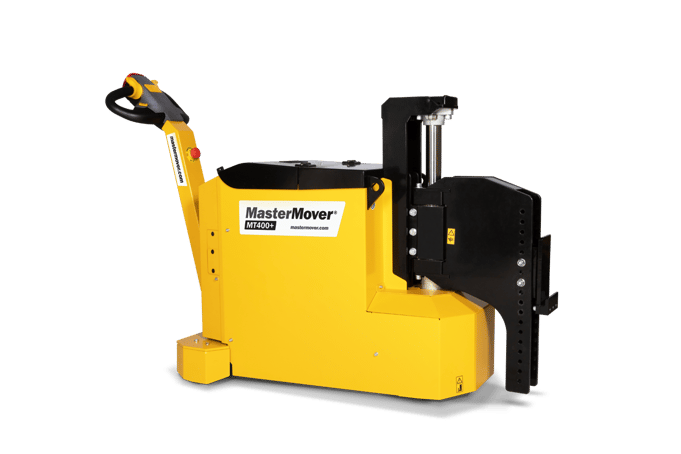
MT400+ Is The Perfect Partner For Lockdown Layout Change
A trailer manufacturer has improved efficiency at its headquarters in France – taking the number of staff needed to move a 4,000 kg load from three people to just one employee.