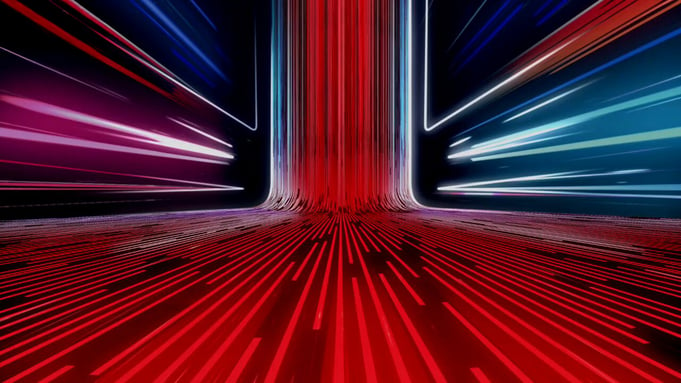
Blog
Welcome to the MasterMover blog, your hub for the latest expertise, industry insights, and essential resources to optimise material handling processes.
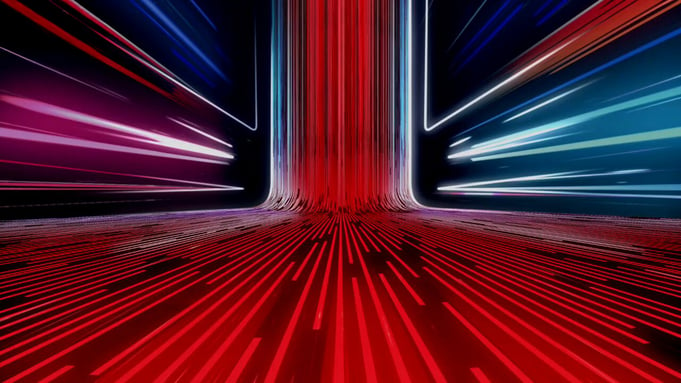
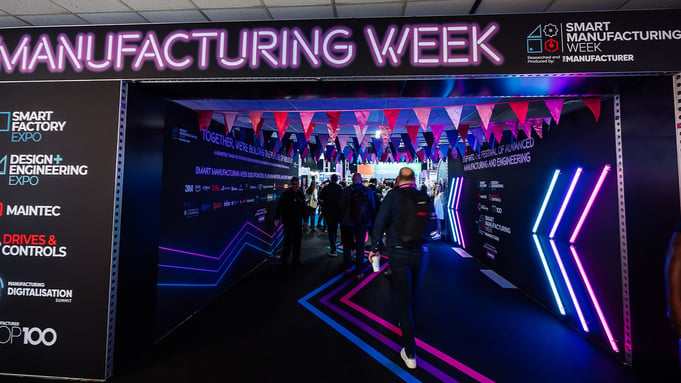
Key trends from Smart Manufacturing Week 2025
Last week we exhibited at the NEC in Birmingham for Smart Manufacturing & Engineering Week, and with reports of over 13,500 attendees, it certainly felt like the place to be for UK manufacturing.
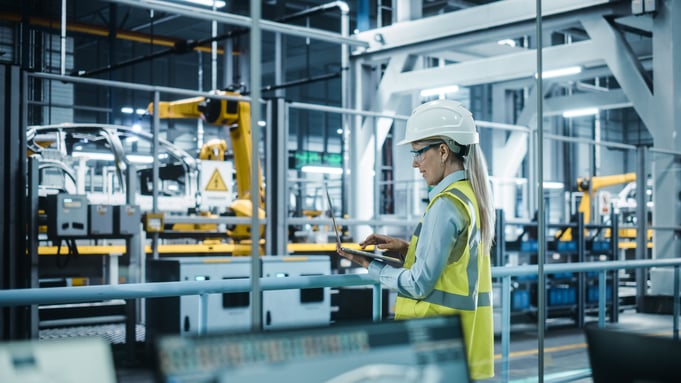
Avoiding the Automation Letdown
The automation buzz is real and uptake is on the rise. Yet many businesses are finding that ‘off-the-shelf' automation solutions—with promises of quick efficiency gains—aren’t quite living up to the hype.
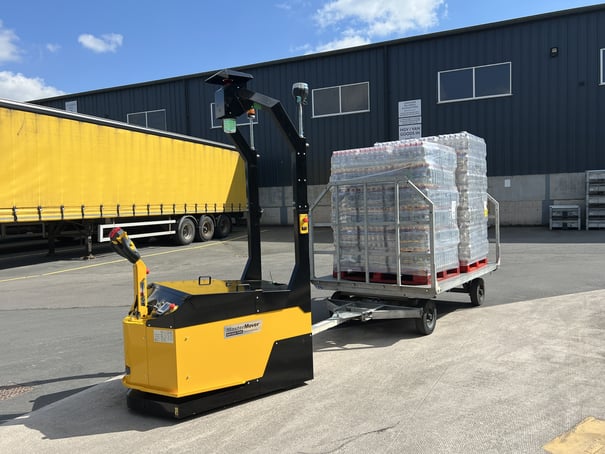
Step Outside to Unlock the Full Potential of AGVs
James Jones Partner Date published: 08/05/2025 Date last reviewed: 03/06/2025 For years, automated guided vehicles (AGVs) have been reshaping internal logistics and manufacturing processes – driving productivity and reducing downtime by moving ...
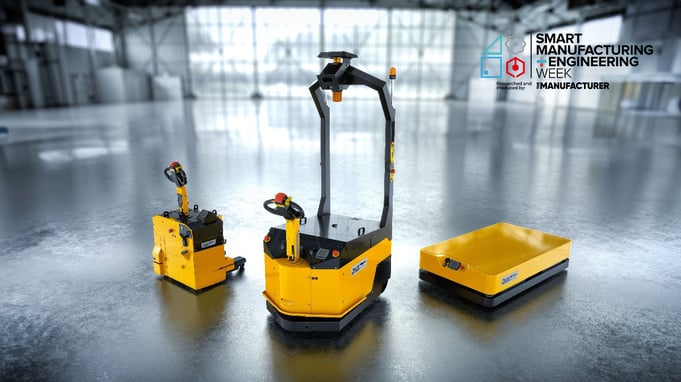
AGVs You Can Trust at Smart Manufacturing Week 2025
We're excited to share that we will be exhibiting at Smart Manufacturing Week again this year at the NEC in Birmingham from 4th-5th June 2025.
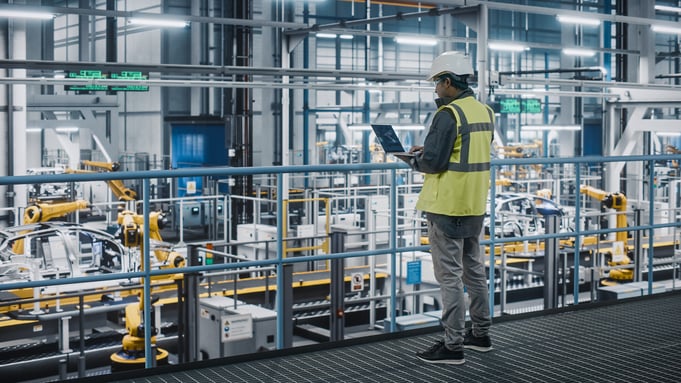
Is your material handling process secretly costing you downtime?
Lucy Cresswell Global Brand Manager Date published: 16/04/2025 Date last reviewed: 16/04/2025 For industrial manufacturers, unplanned downtime is one of the most costly and disruptive challenges. Every minute of lost production can translate to ...
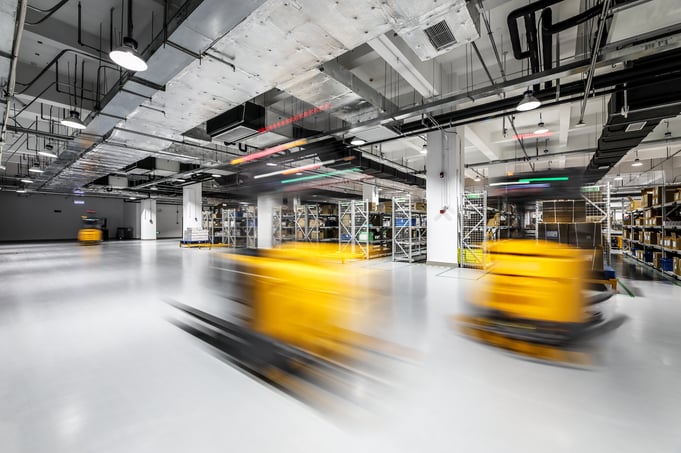
Mythbusting: Is Automation Replacing Humans?
James Jones Partner Date published: 04/03/2025 Date last reviewed: 09/04/2025 There is a shared global cautiousness around automation for many businesses and workers. Yet the reality of robotics and autonomous solutions, such as Automated Guided ...
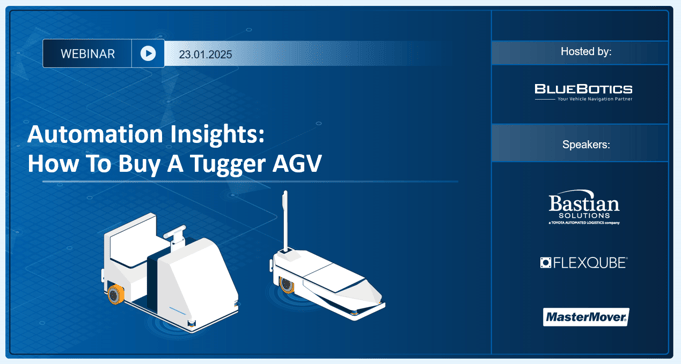
On-demand Webinar: How to Buy a Towing AGV
James Jones Partner Date published: 23/01/2025 Date last reviewed: 01/05/2025 Tugger (a.k.a. towing) AGVs are an efficient way of moving large amounts of material around a plant or warehouse. But what should you consider when selecting a towing AGV?
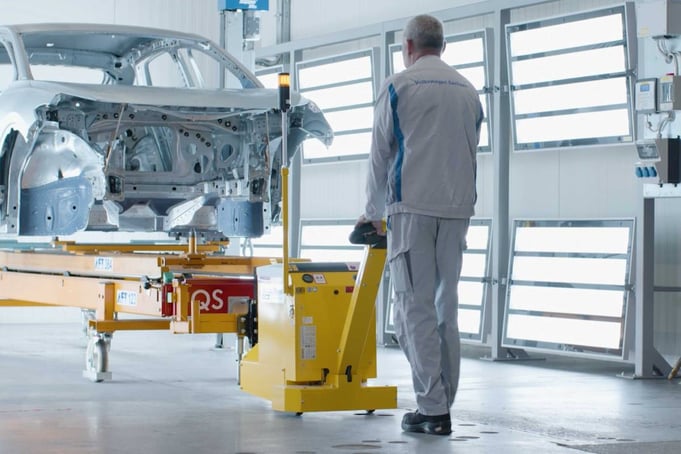
Material Handling Market Set For Major Growth
A market that is undergoing a period of significant growth and transformation is that of material handling. But what exactly is material handling? It encompasses the machinery and tools used to move and store goods during manufacturing, warehousing, ...
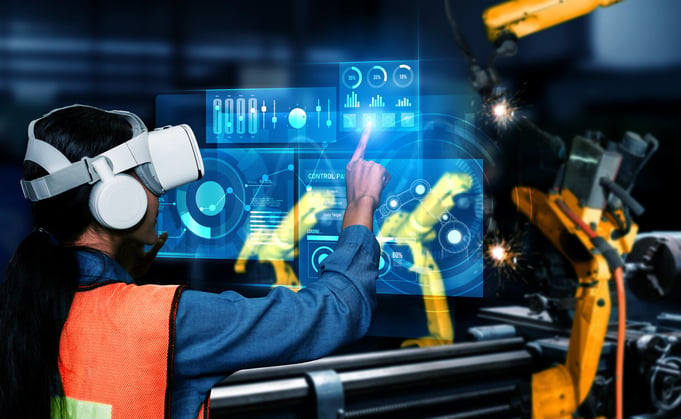
Manufacturing Predictions for 2025
James Jones Partner Date published: 09/01/2025 Date last reviewed: 01/05/2025 As 2025 kicks off, we’re looking ahead to see that manufacturing is on the precipice of a profound transformation. As manufacturers ourselves, we keep our finger on the ...
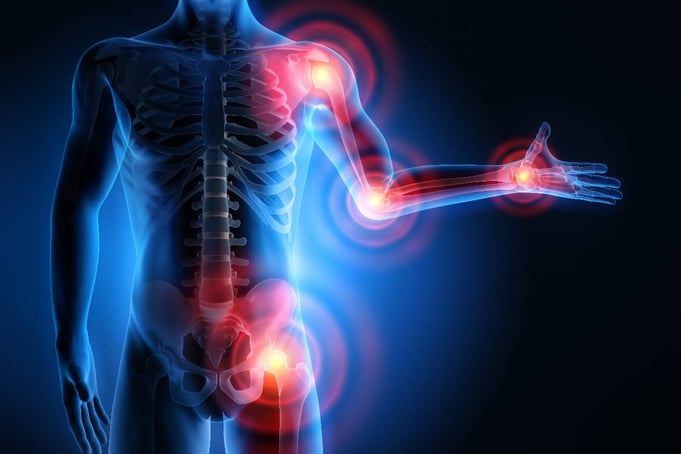
The True Cost of Manual Handling Injuries: HSE 2024 Report Insights
Manual handling tasks are unavoidable for many industries, from manufacturing to logistics to retail. Yet, their potential for causing workplace injuries makes them a critical focus for health and safety professionals. The Health and Safety ...
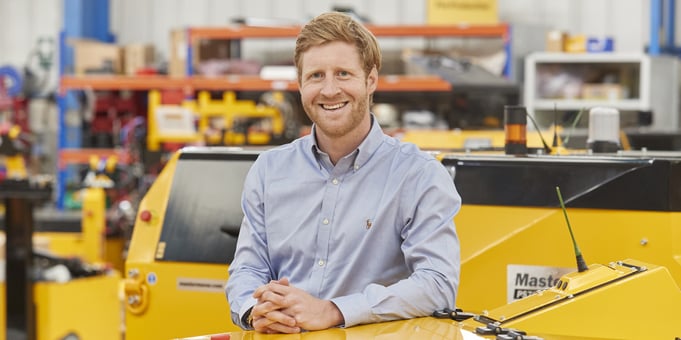
The ultimate tugger AGV guide
James Jones Partner Date published: 23/01/2025 Date last reviewed: 01/05/2025 Tugger AGVs (Automated Guided Vehicles) are becoming an essential tool for businesses looking to enhance efficiency and streamline operations. By automating repetitive ...