Step Outside to Unlock the Full Potential of AGVs
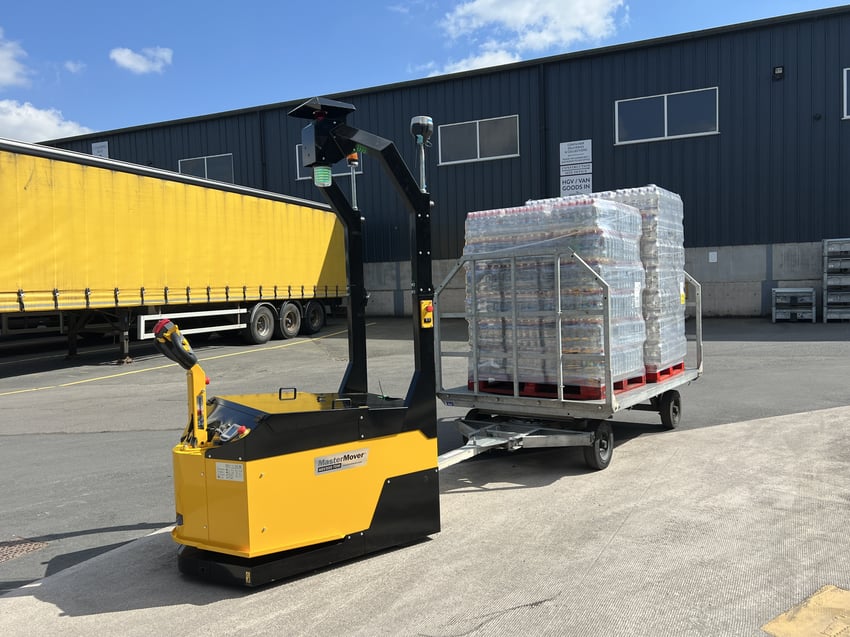
For years, automated guided vehicles (AGVs) have been reshaping internal logistics and manufacturing processes – driving productivity and reducing downtime by moving materials more efficiently.
As suppliers become more innovative and AGV capability is continually improved, the requirements on these machines no longer apply only to indoor processes. Supply chains are interconnected, manufacturing sites are expansive, and the need to move goods seamlessly from one building to another (or even across open yards and external depots) is growing.
Modern industry demands more from automation. Solutions that are multifaceted and able to transition from interior to exterior environments and back without the need for human intervention are needed more than ever.
Traditional outdoor-only AGVs
While indoor AGVs are commonplace, vehicles designed solely for outdoor operation are less so. Robust outdoor AGVs have long performed heavy-duty tasks in environments like seaports, moving colossal containers, and in mining operations, transporting raw materials. More recently, we've seen them enter fields such as agriculture, construction sites, and airport logistics, handling tasks like towing baggage carts or moving large components.
These outdoor-only automation solutions have typically relied on navigation methods suited to open spaces, most notably variants of GPS-based satellite positioning. This works well where there's a clear view of the sky and large, open areas.
Facing a technological hurdle
The real complexity arises when the task is no longer just indoor or just outdoor, but a seamless flow that bridges both environments. Picture an automotive plant needing to move parts from an external storage site to an assembly line inside the factory, or a tyre manufacturer transferring finished stock from production to a separate distribution hub.
Historically, building-to-building transfer has been anything but simple for automation. The issue lies in the fundamental difference between indoor and outdoor navigation technologies, which has often led to operational compromises. Instead of one continuous automated process, companies have frequently resorted to a multi-system approach, for example:
- An indoor AGV moves materials to the edge of the building, near the door.
- A human-operated vehicle (like a forklift) takes over, picks up the load, and transports it across the outdoor space.
- Another indoor AGV at the destination building takes the load for final placement or integration into the internal workflow.
This three-step process introduces manual handling points, creates potential bottlenecks with a reliance on licensed operator availability, increases the risk of errors or damage during transfers, and fundamentally undermines the efficiency benefits that end-to-end automation promises.
Bridging the gap with dual-environment AGVs
The ideal for optimal efficiency is clear: a single AGV capable of navigating autonomously and reliably within a building, seamlessly transitioning to the outdoor environment, moving to another location, and finally entering another building to complete its task. Our MasterMover AGVs are engineered for this.
With the ability to easily manage the demands of busy production environments, our automated material handling solutions ensure smooth operations where space can be at a premium and activity is constant. Our AGVs also confidently handle varied outdoor terrain, slopes, and challenging weather conditions. Built to an IP55 rating, they are protected against rain, meaning operation can continue throughout the year in any weather.
Intelligent design allows our AGVs to adjust their speed in response to adverse weather conditions or reduced visibility, ensuring safety and reliability are maintained. This ability to traverse slopes and manage unpredictable outdoor surfaces is a hallmark of the classic MasterMover durability and high-performance approach, delivering robust solutions for real-world industrial landscapes.
To ensure that the navigational capabilities and safety systems are as sophisticated as the physical engineering of our machines, all MasterMover AGVs utilise BlueBotics best-in-class Autonomous Navigation Technology (ANTdriven by BlueBotics). This industry-leading system provides the precise and dependable guidance required for complex dual-environment tasks, matching the high-performance expectations of our AGVs.
The future is connected
AGVs with true indoor-outdoor capability mark a significant evolution in autonomous material handling. It promises to eliminate inefficient transfer points, reduce reliance on manual labour for repetitive movements, enhance safety by automating both indoor and outdoor traffic, creating truly integrated, end-to-end automation flows across entire sites.
As industries continue to seek greater efficiency, flexibility, and resilience in their operations, the ability of AGVs to step outside and navigate the journey between indoor and outdoor spaces seamlessly will become not just a desirable feature but a fundamental requirement for future-proof automation strategies.
This is the era of dual-environment AGVs, promising a more connected and automated future for logistics and manufacturing worldwide.