Automated Guided Vehicles
Drive ROI, safety and operational efficiency with AGV solutions
Thank you for your request to download the MasterMover 'Guide to Autonomous Guided Vehicles'.
We'll also send you an email shortly with your download link included for safekeeping.
If you do not receive the email, please let us know at salesteamusa@mastermover.com.
Thank you for your request for an AGV System Consultation!
One of our representatives will be in touch with you shortly to discuss your request in more detail.
Fully Autonomous Load Moving
Drive ROI, safety and operational efficiency with AGV solutions
Automated Guided Vehicles (AGVs) have the ability to be transformational when it comes to driving operational efficiency within industrial manufacturing. Featuring best-in-class navigation and safety technologies, AGVs remove the need for human operation, completing movement of products, equipment and materials on time, every time.
This not only makes the operation more efficient but protects your people from the stresses and injuries associated with manual handling, or higher risk load moving solutions. Furthermore, it also means your people can focus on tasks of greater value, driving additional ROI and efficiency.
AGV in Action: Toyota
Learn how Toyota Motor Manufacturing used an autonomous guided vehicle to automate its driving processes.
A world leader in its field, the automotive manufacturer has achieved a return on investment and improved operational efficiency when moving parts to the production line…
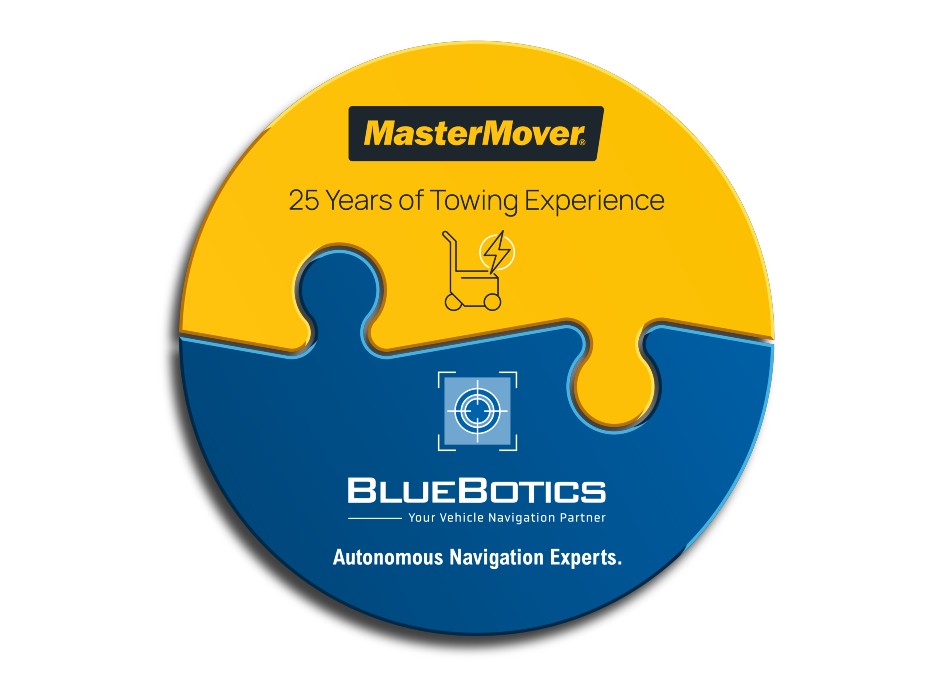
Navigation and machines you can trust
All our AGVs feature BlueBotics best-in-class Autonomous Navigation Technology. BlueBotics encompasses more than 20 years of proven technological experience working with 4,500 products driving more than 6 million miles. No wonder they’re trusted by leading companies the world over.
MasterMover’s high-performance product range delivers all the benefits of our partnership in the form of a robust AGV solution that will boost your ROI now and well into the future.
AGV electric tuggers by range
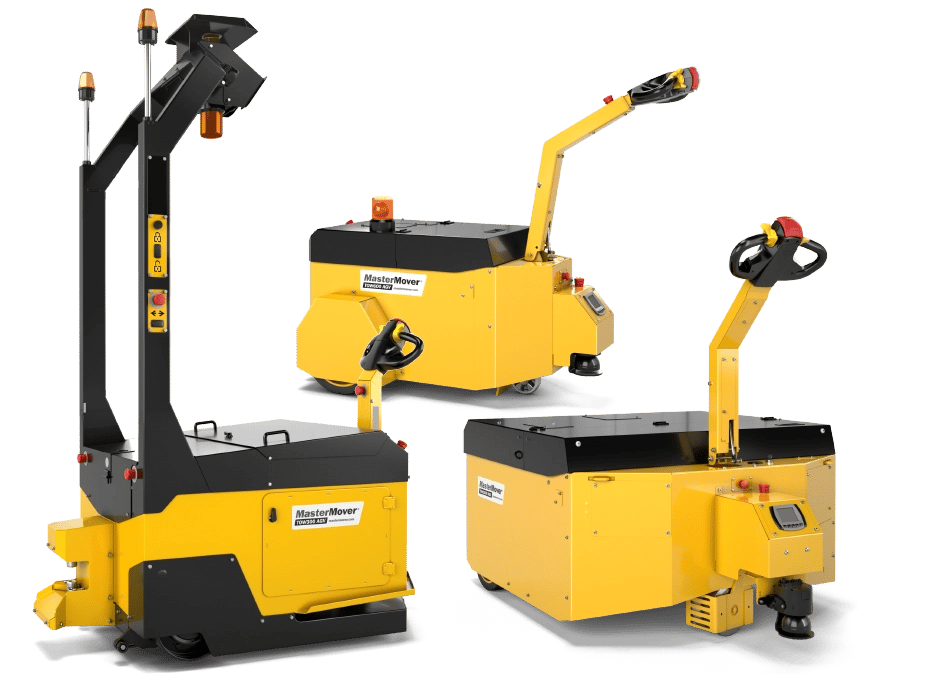
MasterTow AGV Range
Up to 44,000 lbs.
MasterTow AGVs were designed to tow multiple loads with scalable autonomous connecting.
Featuring full natural navigation, they are programmed to integrate with your existing environment like shutter doors and traffic light systems for safe, efficient operation.
Thank you for your interest!
Your requested technical datasheet can be accessed via the button below. A copy has also been sent to you via email.
Please contact us with any questions regarding our products and services, or book in some time to speak with a member of our team.

MasterHandler AGV Range
Up to 13,200 lbs.
MasterHandler AGVs, despite their compact size, are capable of delivering a powerful load-moving performance.
With full natural navigation and compact dimensions, every model performs precise movements, making them ideal for busy and congested environments like modern factories, where safety and efficiency are paramount.
Thank you for your interest!
Your requested technical datasheet can be accessed via the button below. A copy has also been sent to you via email.
Please contact us with any questions regarding our products and services, or book in some time to speak with a member of our team.
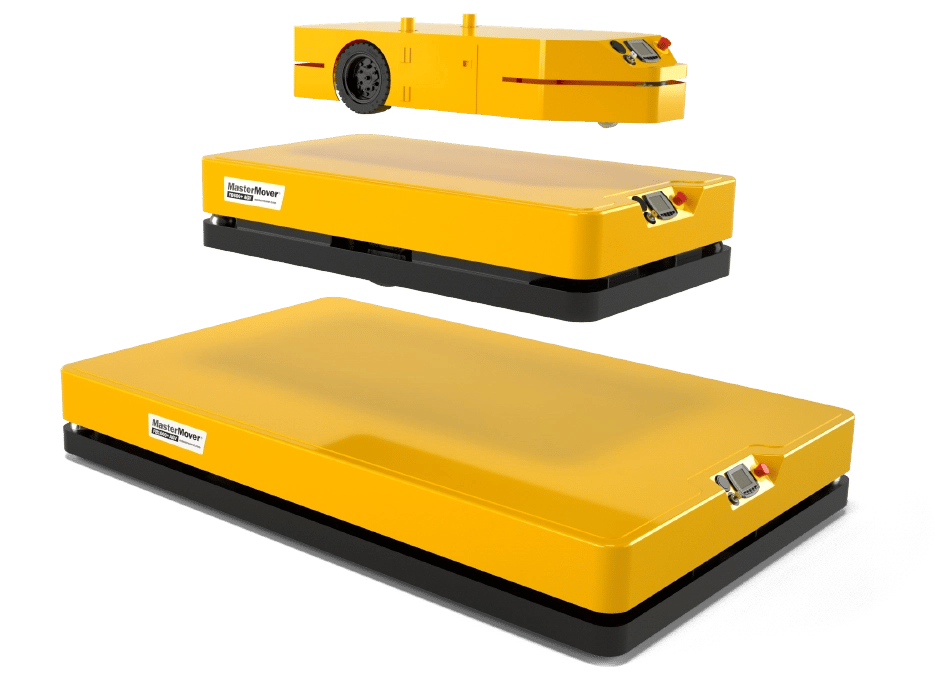
Flatbed AGV Range
Up to 22,000 lbs.
Unlike competing large and cumbersome units, our Flatbed AGVs are quality load carriers that are built to last.
Our AGVs are highly maneuverable and can pivot on the spot, making them ideal for working in tight spaces. Seamless integration enables ultimate efficiency and safety in any environment.
Thank you for your interest!
Your requested technical datasheet can be accessed via the button below. A copy has also been sent to you via email.
Please contact us with any questions regarding our products and services, or book in some time to speak with a member of our team.
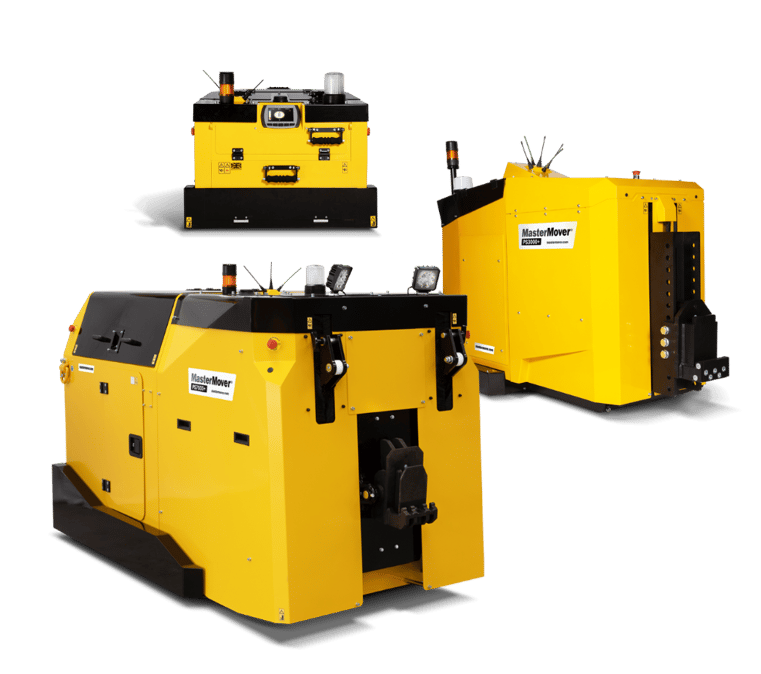
PowerSteered AGV Range
Up to 154,000 lbs
Our PowerSteered AGVs are trusted by industrial manufacturers to deliver the autonomous movement of the heaviest payloads.
Your choice for heavy weight AGV capabilities, the PowerSteered AGV range drives efficiency and repeatable processes across heavy industry.
Built with benefits to supercharge your processes
Increased Return on Investment
AGVs deliver greater ROI through increased efficiency and safety, better use of people resources, less risk of mechanical failure and greater flexibility.
Maximum Safety Built-In
With in-built safety systems, environmental scanners, and optimum surrounding awareness – increased safety comes as standard.
Efficiency Supercharged
Drive operational efficiency by completing tasks on time and at optimal speed. Enjoy flexible layouts without the constraints of fixed infrastructure.
Scalable Pulling Power
Our AGV systems are available with a capacity up to 30,000kg, enabling automated movement of even the heaviest of loads.

Delivering return on investment
An AGV can reach an ROI of between 50% and 150% when used for a single-shift over 3 years.
This can be dramatically increased to over 600% when the machine is used as part of a three-shift operation over a 5-year period.
An AGV that fits your application
Regardless of your current phase, we understand that switching to an automatic towing system is an investment, even if it is one that will inevitably deliver increased ROI, efficiency and safety. Our skilled and experienced team is here to guide you with our tried and tested approach.
Our 5-step process:
Thank you for your request to download the MasterMover 'Guide to Autonomous Guided Vehicles'.
We'll also send you an email shortly with your download link included for safekeeping.
If you do not receive the email, please let us know at salesteamusa@mastermover.com.
-
1. The right machine for you
First, we put time into understanding your application.
-
2. The right navigation for your site
We’ll explore which navigation system works best.
-
3. The right dispatch commands
Next, our team will look at how the AGV gets its instructions to move or ‘pulse’ to the next location.
-
4. Integration with your systems
Then, we look at where other system integrations are needed.
-
5. Optimize your safety systems
Depending on the environment and application, identifying the right safety systems is key.
The ultimate guide to AGV electric tuggers
Automated Guided Vehicles (AGV)
Looking to understand Automated Guided Vehicles in a little more detail?
We’ve compiled some helpful resources to get you started, covering everything you need to know.
Why we're different. Our AGV capability
Weight Capacity
Our AGVs move up to 66,000 lbs., enabling automated movement of even the heaviest loads.
Speed
MasterMover AGVs travel up to 8 feet per second even with heavy loads.
Terrain
They’re designed to travel inside, outside, in the rain, and even on slopes.
Durability
All MasterMover products are manufactured to the highest standards. They are reliable, durable and dependable.
Dual Mode
They can also be assigned to other tasks and jobs, helping to drive additional ROI and flexibility.
Intelligence
Our AGVs do not rely on WiFi to operate, like many other AGVs.
Battery Capacity
We built in a runtime of 10 hours with a single battery and 24 hours using multiple batteries, so operational efficiency is maximized.
Custom Solutions
Our in-house team can design and build custom solutions in stainless steel and to specific environmental standards, if required.
Answering your AGV questions
- Line follow: A painted or magnetic line on the floor.
- The AGV follows only the painted or magnetic line (including markers to tell it where to stop or change direction).
- Natural: A navigation that requires no external infrastructure.
- The AGV maps its surroundings using sensors during training runs and stores the data onboard.
For many people, AGVs are still unknown and so it’s no surprise that people ask “What is an AGV?'.
Sometimes referred to as autonomous guided vehicles, automated guided vehicles (AGVs) are a type of material handling system that travel autonomously - without the need for an operator or driver. As a self-guided vehicle, they improve efficiency and material flow by automating repetitive tasks. A range of different types of automatic guided vehicles exist including forklift AGV systems, towing AGV and tugger AGV systems, unit load AGVs, automated guided cart systems and automated load carriers.
A towing AGV system enables businesses across industrial manufacturing and logistics to drive operational efficiency, increase resource utilization and reduce non-value-adding tasks in their material handling processes.
With the rise in industrial automation, many businesses look to automatic guided vehicles to streamline the movement of heavy materials and loads, eliminating the need for human involvement.
If you're interested in an automated guided vehicle system or autonomous vehicles, you're probably wondering what industries use them. Automation and automated equipment are becoming increasingly more accessible and the adoption of automated technologies is no longer just seen in automotive environments.
Our AGV systems are used across industrial manufacturing, from plastics and metal manufacturing to automotive assembly.
Likewise, the repetitive nature of intralogistics processes in distribution and logistics continues to drive an increase in warehouse automation systems and automated guided vehicles.
Automated guided vehicles (AGVs) and autonomous mobile robots (AMRs) differ primarily in their navigation capabilities.
AGVs rely on pre-defined routes or markers to follow a fixed path within a controlled environment, requiring physical infrastructure for guidance. In contrast, an autonomous mobile robot utilizes advanced sensor systems and algorithms to autonomously navigate without the need for fixed infrastructure or predetermined routes.
AMRs can perceive their surroundings, avoid obstacles, and dynamically plan paths in real time. AMRs are most commonly used to move lighter loads, with the most common design being a unit carrier or load carrier.
Our advanced AGVs feature best-in-class Autonomous Navigation Technology (ANT) by BlueBotics. ANT natural navigation requires no external infrastructure. Using sensors, the AGV maps its surroundings, during training, resulting in no need to reconstruct warehouse or production environments.
Our AGV integrates sensors and various components that receive, process and analyze data in real time and act accordingly. When an autonomous guided vehicle encounters an obstacle on its route, such as a pallet or person, it will stop if it detects that it could harm the operators.
The different types of AGVs and their corresponding navigational methods dictate the ease of installation. For example, a line following system, an AGV system in its’ most simplistic form, enables simple cost-effective installation by simply sticking a line of tape that the machine follows.
For more complex systems, a reputable supplier will work with you to arrange installation at your site.
AGV perfectly complements your existing workforce. AGVs do the heavy manual work, Removing or reducing the need for your staff to move materials, allowing your people to spend more time doing greater-value tasks.
Natural navigation requires no external infrastructure. Using sensors, the AGV maps its surrounding, during training, resulting in no need to reconstruct warehouse or production environments.
Our AGV navigation technologies include:
Our AGVs, unlike others, are built to operate indoors, outdoors, on slopes, uneven terrain and even in the rain, ensuring production and manufacturing processes can reduce downtime with autonomous load moving between buildings.
MasterMover AGVs travel up to 2.5m per second, even with heavier loads. AGVs are capable of adapting to the surrounding environment, slowing down at certain points i.e. through high pedestrian areas and then speeding up when necessary.