Hayward Tyler: Electric Tugs Eliminate Need for Forklifts
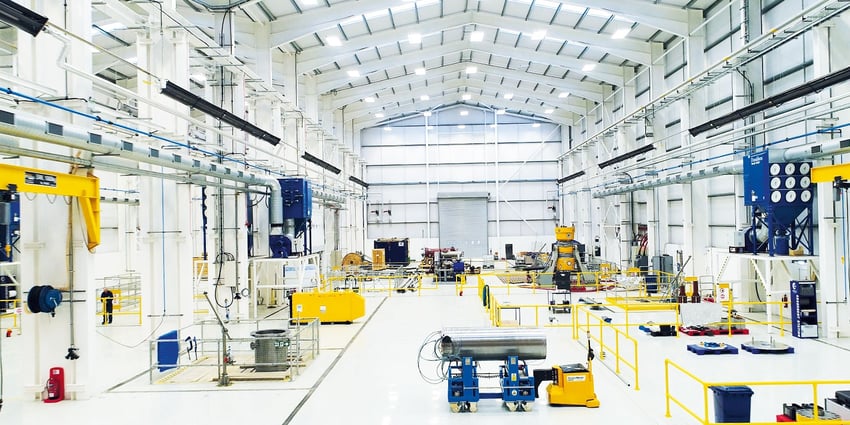
Hayward Tyler creates leaner, more efficient flowline production systems using the MasterTug range. Driving more flexible processes, the manufacturer has seen a significant reduction in overhead crane and forklift use, improving safety and maximising efficiency.
Hayward Tyler is a global market leader in the manufacture of performance critical electric motors and pumps. Variations of applications and environments determine their shape, size, and weight.
The specialist motors and pumps can vary in size up to 6 metres in length, 1.5 metres in width and weigh up to 40 tonnes. Such variations can present a logistical challenge within production processes thus requiring a solution to establish methods for moving products with different specifications whilst maintaining flow efficiency.
Moving motors was a slow process
Hayward Tyler previously used an overhead crane to lift motors/pumps and lower them onto trestle frames. Individual or groups of engineers would then work on or add components to the motor/pump before it was transferred to a successive work station.
Transfers were frequent and would not always flow in the same direction. At sections where the two parallel overhead cranes did not meet, a forklift would be used to transport motors/pumps between cranes. This slowed the manufacturing process, reduced efficiency, and increased costs.
Time to change
Hayward Tyler has adopted a more efficient ‘flowline’, by adopting a single piece process perfected by the aerospace industry. All workstations follow a straight line and continue on from each other successively. This means that the base product starts from one end and is completed at the other end of the workshop floor.
Despite changing the flow of work, it was envisaged that overhead cranes would still be used for frequent lifting and moving.
To reduce the need for transporting products between work areas and allow for more tasks to be performed at each station, Hayward Tyler developed a series of patented ‘intelligent’ workstations. Referred to as Crusers by the company, these bespoke pieces of equipment hold the motor/pump.
In addition to providing support for them, individuals are also able to alter the height of the workstation or rotate the product. This allows the engineers to complete more tasks at a single workstation with increased safety and ease. Making the Crusers manoeuvrable has further reduced the need of overhead cranes.
This led Hayward Tyler to discover MasterMover.
“The need for manoeuvrability led us to explore options for locomotives or electric tugs that could attach to the Crusers. The challenge was to find a reliable propulsion system that could handle the weights, allowing precision manoeuvres.”
Oliver Buhlinger, Continuous Improvement EngineerHayward Tyler
Mastering a solution
MasterMover’s MT1500+, with its impressive specifications and the capability to move wheeled loads weighing up to 15,000kg, was presented as an ideal solution. To compare options, the MT1500+ was tested against a competitor’s tug.
Both machines were used to transport a 9,700kg load. Oliver explained that “the key benefit of the MasterMover tug was the manoeuvrability. The emergency stop button could bring the machine and load to an immediate halt safely and the operation was very smooth. Hayward Tyler’s operators were given a customer questionnaire and the results meant we just ‘had to go’ with the MasterMover tug.”
Hayward Tyler purchased the MT1500+ and went on to order an additional MT2000+ for loads of up to 20,000kg on castors and 80,000kg on rails.
By utilising electric tugs to drive more flexible processes, the manufacturer has seen a 50% drop in the use of overheads cranes and a significant reduction in the use of forklifts, both of which drastically boosts productivity, and ensures a safer workplace.
What’s more, the need for a forklift to bridge the gap between two cranes has been eliminated completely. Hayward Tyler is now forklift-free in pedestrian areas. This aids in meeting the 'Fit for Nuclear' safety requirements, as Hayward Tyler is part of the Civil Nuclear Sharing in Growth programme.
Such is the success of the Cruser and MasterMover electric tug combination that Hayward Tyler is already looking for further expansion of the product and expanding its application into other areas of manufacturing using its Luton based Centre of Excellence as a ‘shop-front’ for the art of the possible.