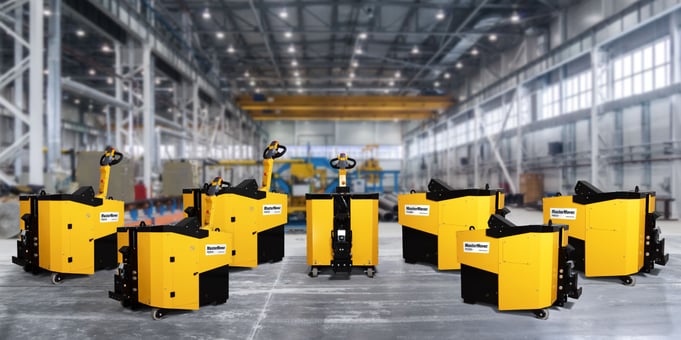
MasterMover Global News
Explore the latest news from MasterMover to keep up to date with exciting developments, insightful updates and company announcements.
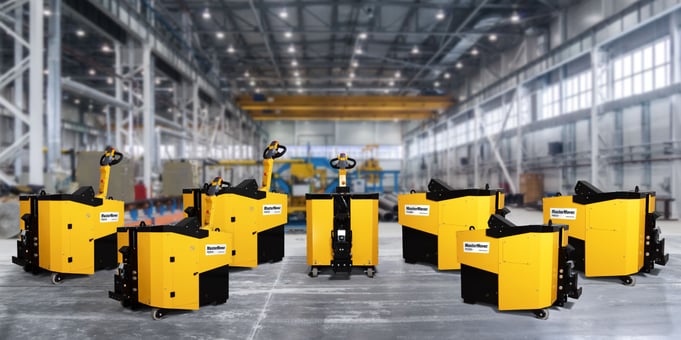
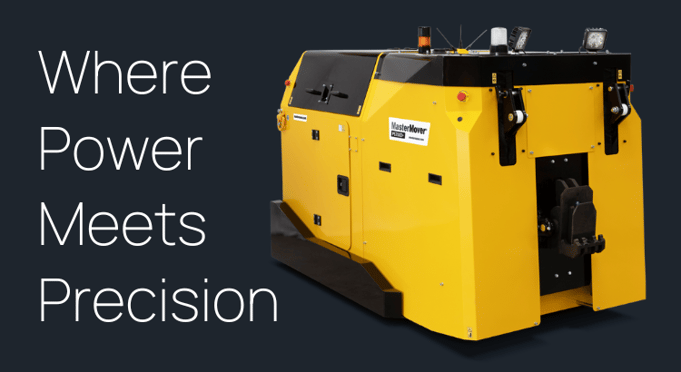
MasterMover Launches World’s Most Powerful Electric Tugger Solution
MasterMover, the global leader in electric tug solutions, has announced the launch of its new remote-controlled PS7000+ model, featuring an impressive load-moving weight capacity of 154,000 lbs. and patented MultiLink technology.
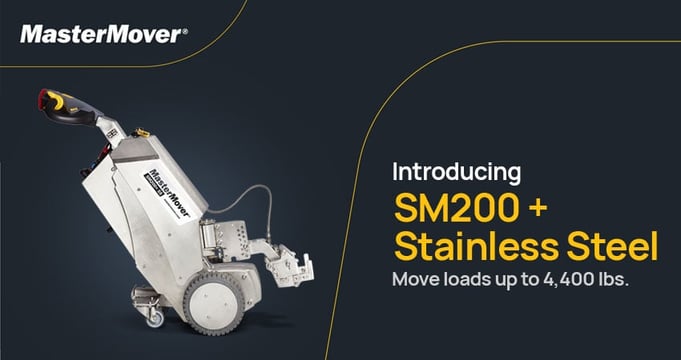
Stainless Steel Tugger Range Expanded with 4,400 lbs. Capacity Model
MasterMover, the global leader in electric tugger solutions, has launched its new SM200+ SS model, designed to deliver the safe and controlled movement of heavy, wheeled loads in cleanroom and food-safe environments.
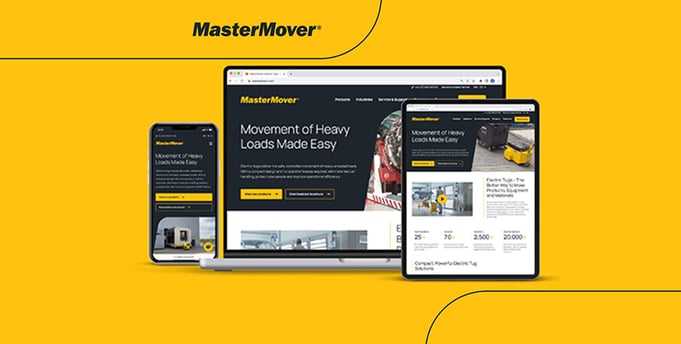
Unveiling Excellence: Our Refreshed Brand and Innovative Website
Introducing our newly updated brand identity and cutting-edge website, a true testament to our unwavering dedication to providing exceptional customer experiences. At MasterMover, we have reimagined our entire image and online platform to enhance ...
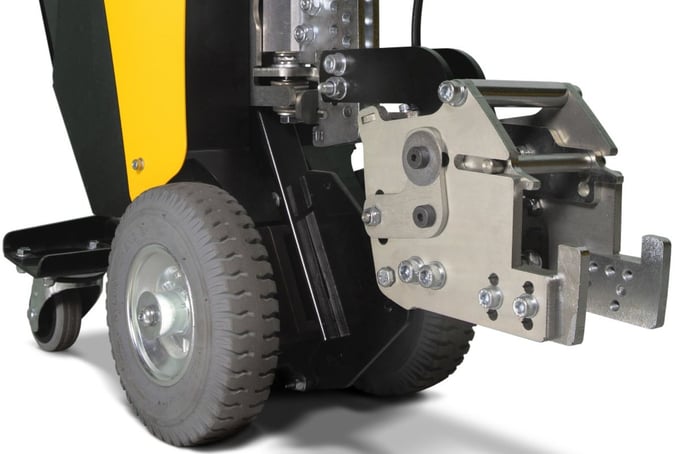
MasterMover Introduces LogisticsMover Electric Tugger
MasterMover, the award-winning manufacturer of electric tugger solutions, has announced the latest addition to its growing product portfolio with the introduction of the LogisticsMover (LM100) as part of its SmartMover range.
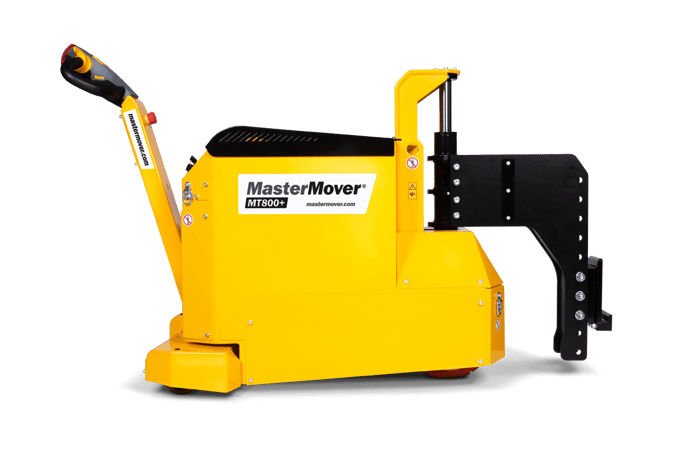
MasterMover Updates to the MasterTug Range
MasterMover, the award-winning manufacturer of electric tugger solutions, has announced significant updates to its MasterTug range, used worldwide by some of the leading names in Industrial Manufacturing industries.
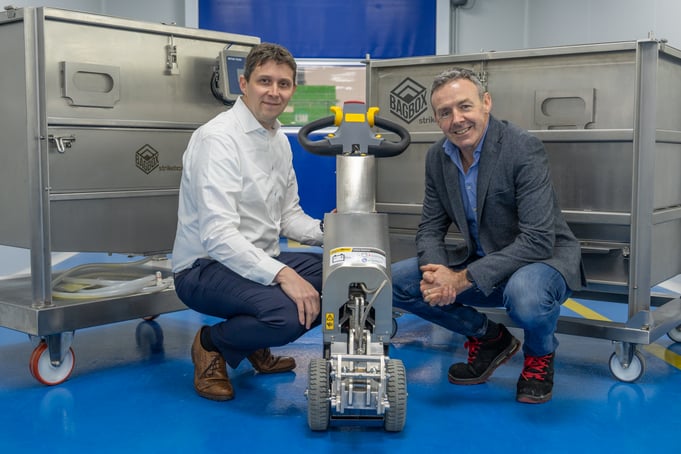
Strikebox Engineering Partners with MasterMover for Cleanroom Equipment
Strikebox Engineering, headquartered in Ireland but servicing a global customer base, has entered into a partnership with electric tug manufacturer, MasterMover. The agreement will see Strikebox offer the MasterMover range of best-in-class stainless ...
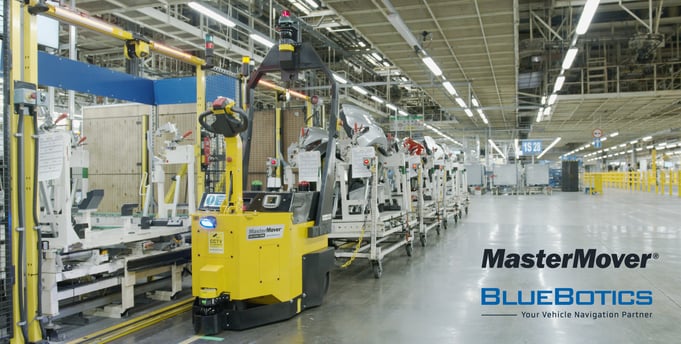
MasterMover Partners with BlueBotics for Best-in-Class AGV Navigation
MasterMover, the world’s leading manufacturer of electric tug and tow solutions, has announced a new partnership with vehicle automation leader BlueBotics to provide best-in-class ANT navigation technologies for MasterMover’s range of Automated ...