Hörmann Unlocks The Benefits Of Seamless Production
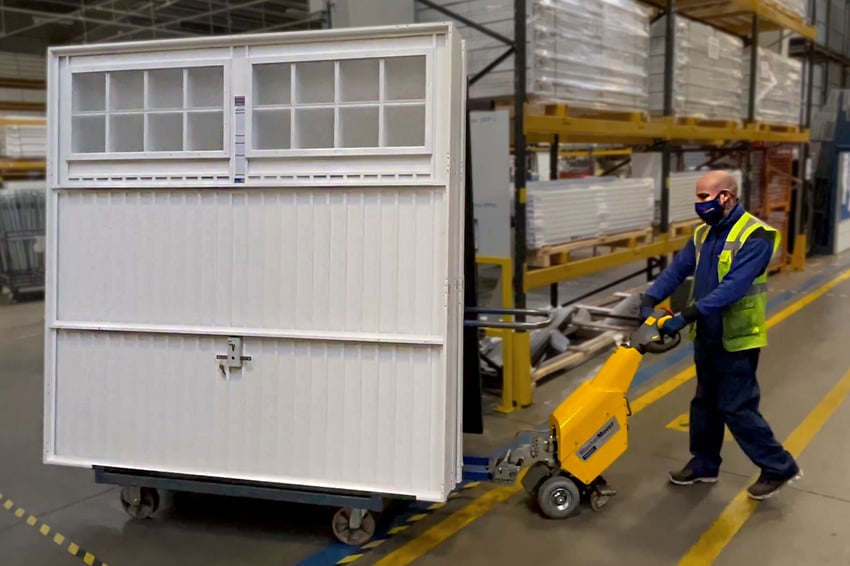
Keeping production running smoothly and without interruption is a priority for Hörmann UK.
The Leicestershire-based business is the market leader in garage doors and assembles thousands of canopy and retractable up-and-over doors every year.
A heavy challenge
From warehouse to production line, components are moved on an A-frame trolley over a distance that takes around 15 minutes on foot and can weigh up to 1,000 kg.
As Facilities & Maintenance Manager Eliot Buckby explained, it would be an impossible task to undertake manually:
We generally pick between 300-400 panels per day so an electric tug is really the only way to move the components on the trolley over the distance that's required. It couldn't be done at the volume that's needed by hand.
Eliot BuckbyFacilities & Maintenance Manager, Hörmann
He went on to further explain that "a forklift or other method also wouldn't be suitable as there are many aisles in the production area to navigate. We need manoeuvrability and flexibility."
A smart solution
With MasterMover's SmartMover machines now deployed at the site, the team at Hörmann can easily move these heavy trolleys throughout the production area as the machine is compact and designed specifically to tackle tight spaces.
The SmartMover also has robust yet simple coupling systems to ensure that Hörmann's loads are secure and gives operators complete control, even on slopes. Safety-focused, the production team now benefit from anti-crush functionality, emergency stop, variable speed settings, and intuitive controls to keep operators, loads and equipment safe.
To enable the busy factory to meet demand, the team now use two SM100+ machines in rotation.
After implementing the SmartMovers into their production processes, Eliot confirmed that "a SmartMover does exactly what we need it to and the ability to easily swap the lightweight batteries over is a massive advantage to allow for continuous production.
"We've used the SmartMovers in our goods-in areas also - because of the machine's flexibility we can move it to where we need it to go very quickly and with no issues. Using the SmartMover has removed a lot of our manual handling issues. The machines are very easy to use and store and I would highly recommend."
It's vital for busy and crowded production sites to provide their team with the right equipment to maximise productivity and safety. Working with a genuine industry expert guarantees that premium material handling equipment will always outperform.