From Factory to Launchpad – Pinpoint Accuracy for Satellite Facility
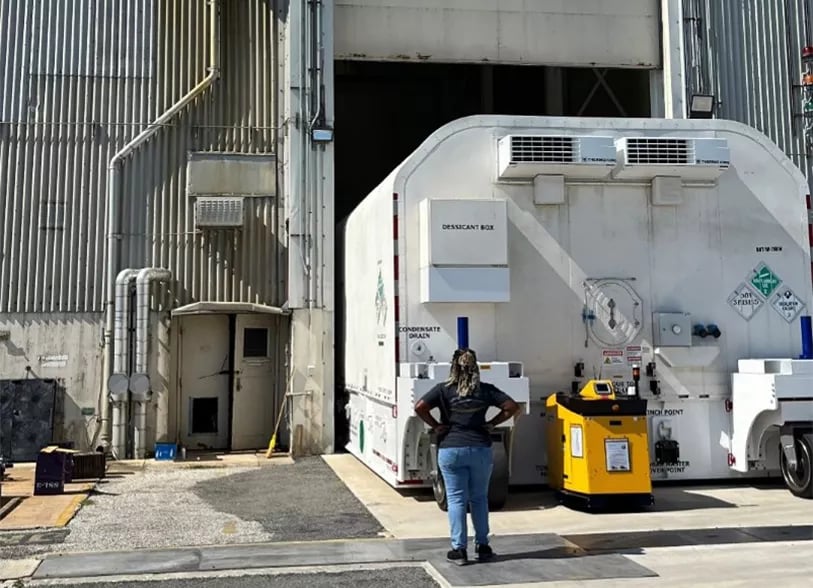
Discover how a leading manufacturer of space technology moves satellites weighing almost 110,000 lbs. with an innovative solution from MasterMover.
The challenge: moving communication satellites
The successful launch of communication satellites is pivotal in maintaining global connectivity and advancing scientific research. Used across Earth monitoring, defense, communications, and space exploration, satellites are crafted with meticulous precision. However, the technological nature and sheer size of satellites can challenge transportation.
A leading space technology company specializing in the manufacture of communication satellites faced the formidable task of moving 110,000 lbs.satellites through their manufacturing process, across their facility, and at rocket launch locations.
Before implementing an electric tugger solution from MasterMover, satellites were previously moved using large, ride-on diesel towing tractors – but with larger satellites weighing almost 110,000 lbs, the towing tractor lacked the power and finesse needed to complete movements safely. Alongside a need for a more robust solution, this manufacturer needed a solution that addressed the challenges of:
- Limited visibility: Moving the satellites with a large diesel towing tractor resulted in poor driver visibility, which was a key concern considering the size of the loads being moved.
- Inefficiency: The previous process was time-consuming, requiring multiple spotters and continuously stopping and starting movement to ensure the necessary clearance in tight areas.
- Tight spaces: The movement of satellites between different stages of manufacturing involves navigating tight spaces with minimal clearance between fixed infrastructure and equipment - requiring a solution for controlled movement in confined areas.
- Risk of damage: Moving large high-value loads in tight spaces with poor visibility leads to the risk of damage to satellites, equipment, and facilities. With damage that can cost hundreds of millions of dollars per satellite, reducing this risk through accurate, controlled movements was a key priority.
For this manufacturer, the process of moving a satellite through production involves navigating a series of tight turns where clearances between the load, other equipment, and infrastructure are tight. Moving the load with the incumbent ride-on towing tractor resulted in poor visibility during movement and the risk of damage. Assessing the challenges of their current process, this space technology manufacturer approached MasterMover to investigate a solution.
“For this customer, it was clear we had a solution that we could build on to meet their exact requirements. When you’re moving satellites several times a week through tight areas in production, and any damage to a satellite could easily cost millions of dollars, it’s clear that a solution needs to be able to move loads precisely every time.”
Andy Owen, President
Stellar Solution for Satellite Move with MultiLink Technology
Working with MasterMover’s Custom Engineering team, a MultiLink system – combining two PS3000+ machines was recommended. With MultiLink technology, multiple machines can work in synchronization under the control of a single operator.
Enabling multiple electric tuggers to work together, MultiLink solutions deliver unrivaled weight-moving capacity, combining the power of multiple tugs. For this manufacturer, a MultiLink solution using two PS3000+ was recommended to provide the performance to safely maneuver the satellites in the yard and at rocket launch locations.
Remote Control Operation at Launch Locations
The movement of satellites stored in large transport boxes at launch locations is typically carried out twice a year. Alongside the benefits of precise movement and maneuverability, the remote-control operation enables an operator to walk around the load, monitor blind spots and ensure the necessary clearance during movement, reducing the risk of collisions when moving satellites out of the facility and at rocket launch locations.
Taking Accuracy to New Heights with Semi-Automated Solution
To reduce the risk of damage, the California-based satellite manufacturer wanted to explore the potential of partially automating the movement, enabling machines to follow pre-defined paths through the facility.
The movement involves maneuvering satellites through manufacture with minimal clearance between the load and walls. To eliminate the risk of accidental damage in such tight areas, MasterMover incorporated Line Follow navigation into the solution.
With the solution in place, operators use the remote control to position satellites onto the magnetic strips on the floor and simply switch the machines into automatic mode, with the machines then continuing the movement autonomously. By following predefined routes, the machines ensure accurate movement – every time, reducing the risk of human error or accidental collisions in tight areas.
The most unique part of the solution is around the Line Follow technology used on this application. Line Follow systems typically involve a single machine following a magnetic strip on the floor. In this instance, the sheer size of the load and the confined nature of the environment meant that the PS3000+ machines needed to follow two separate paths to facilitate the tight turns required for the operation.
“The clever part about this application is that the two machines had to work together but follow two separate paths so that the satellite could make the tight turns. Normally, a Line Follow system would involve one machine following what is effectively a magnetic train track.
In this case, we've got a MultiLink system following two separate magnetic strip routes – which is something specifically designed around this customer’s requirements and very unique. It really showcases MasterMover’s custom engineering capability”.
Andy Owen, President
Results and Benefits
Having implemented the MultiLink solution with Line Follow navigation for the movement of high-value satellites, this space technology manufacturer benefited from:
Precise Movements: When using Line Follow navigation, the machines can adhere to predefined paths with millimeter-level accuracy. This capability ensures that satellites are transported through tight spaces and narrow passageways with complete accuracy.
Cost Savings: By reducing the risk of satellite damage costing hundreds of millions of dollars per satellite, the company has saved a significant amount in potential repair costs.
Maximum Visibility: For the movement of satellites in the yard and at launch locations, operators use the remote-control operation to safely move and position loads with maximum visibility.
Heavy-Load Capacity: Unlike the previous ride-on towing solution, the PS3000+ MultiLink solution is engineered to handle the increasing weight of satellite products. A robust design enables them to easily transport the heaviest satellites.
Improved Efficiency: Streamlining manufacturing and launch processes, the PS3000+ solution delivers significant time savings compared to the previously time-consuming ride-on towing equipment.
The MasterMover PS3000+ MultiLink solution and Line Follow navigation have proven to be indispensable for this satellite manufacturer. Delivering millimeter accuracy, controlled positioning and the ability to handle heavy loads, the solution has significantly improved safety and control. The company is confident that the solution will continue to play a critical role in its operations for years to come.