Moving Wind Turbine Blades During Manufacturing
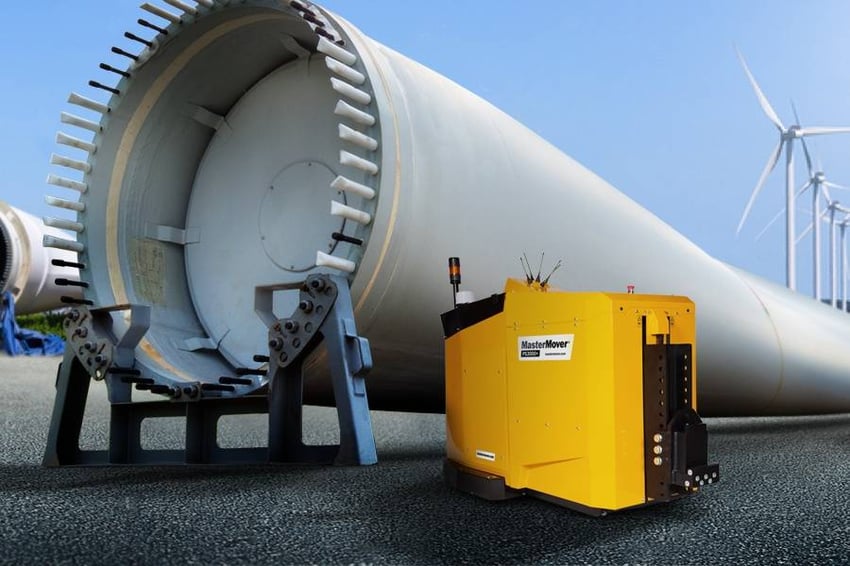
Moving wind turbine blades during manufacturing can be a difficult task. In industrial applications, they can reach up to 100m in length (in fact the world’s largest is 107m long), and weigh many tonnes.
Their size and weight pose challenges when moving wind turbine blades during the manufacturing process. However, that is where MasterMover electric tugs come in…
Introducing Electric Tugs & MultiLink
Our electric tugs have the capacity and power to handle the weight of wind turbine blades, making it possible to move them safely and efficiently during manufacturing.
For example, our remote-controlled PS3000+ model can handle up to 30 tonnes. But our MultiLink technology allows multiple electric tugs to be synced together and controlled by a single operator. This means an electric tug solution can handle well over 100 tonnes effectively, delivering safe and efficient movement even at extreme sizes and weights.
This technology is especially useful when handling a load such as a wind turbine blade, which are clearly long in terms of size profile. MultiLink allows electric tugs to be positioned at each end of the wind turbine blade, or at suitable points depending on the manufacturing platform.
Controlled Movement in Any Direction
A further benefit that MultiLink offers relates to the direction of travel.
With a single electric tug, a load is moved like that of a truck and trailer. The load is moved forwards and backwards and turns as per the requirement, but the single drive point determines direction of travel.
However, with multiple electric tugs working in sync, operators have total freedom of movement, allowing the wind turbine blade to additionally be moved sideways, rotated, or navigated around a defined point. Very helpful when moving such a large profile load – especially one as valuable as a wind turbine blade – as the ability to carry out difficult manoeuvres is made far easier.
Due to our SmartCoupling capabilities, each electric tug knows where it is connected to the load. It can therefore apply the relevant ‘steer maths’ to ensure the set of tugs work in unison, moving together and applying the relevant levels of force depending on direction of travel.
Flexibility to Handle a Range of Tasks
An additional benefit of using electric tugs to move wind turbine blades during manufacturing is that, whilst MultiLink technology allows multiple tugs to be used together, the electric tugs themselves can be also used independently at other times.
Need to move a load of 20 tonnes? That’s not problem…simply use a single electric tug independently for this task.
This adds value to the operation by delivering a material handling solution that can carry out wide range of jobs, driving return-on-investment as the electric tugs are used more often, for more tasks.
Safety in Focus
As with all MasterMover electric tug solutions, safety is always our focus. Our applications to move wind turbine blades are no different.
The Remote-Control unit features emergency stop functionality, which is also present on each electric tug itself. Furthermore, a separate emergency stop controller can be used, where an independent ‘banksman’ can take up a different vantage point and cut power to all units at the touch of a button.
The use of Remote Control for movement is also a safety feature in itself, with the operator able to take up the ideal viewing position to identify obstacles and threats.
In addition to a variety of other safety features such as warning lights, electric tugs moving such weights utilise hydraulic coupling systems. This ensures the connection to the load is secure, and load safety is maximised.
Summary of Key Points:
- MasterMover electric tugs have the power and capability to move loads of 100 tonnes plus.
- MultiLink enables multiple electric tugs to synchronise and work together.
- Using multiple electric tugs together offers total freedom of movement offering safety for operators, the blades, and the surrounding environment.
- Emergency stop functionality delivers an additional layer of protection, and is available on the electric tugs, on the Remote-Control unit, and additional via an independent ‘banksman’.
- Electric tugs can be used independently to fulfil a variety of other material handling requirements.
- The PowerSteered range is Remote Controlled, allowing the operator to take up the ideal vantage point.
If you’re looking for a safe and efficient way to move wind turbine blades during manufacturing, as well as smaller materials associated with the operation, look no further than MasterMover electric tugs.