4 Common AGV Myths
AGV Systems
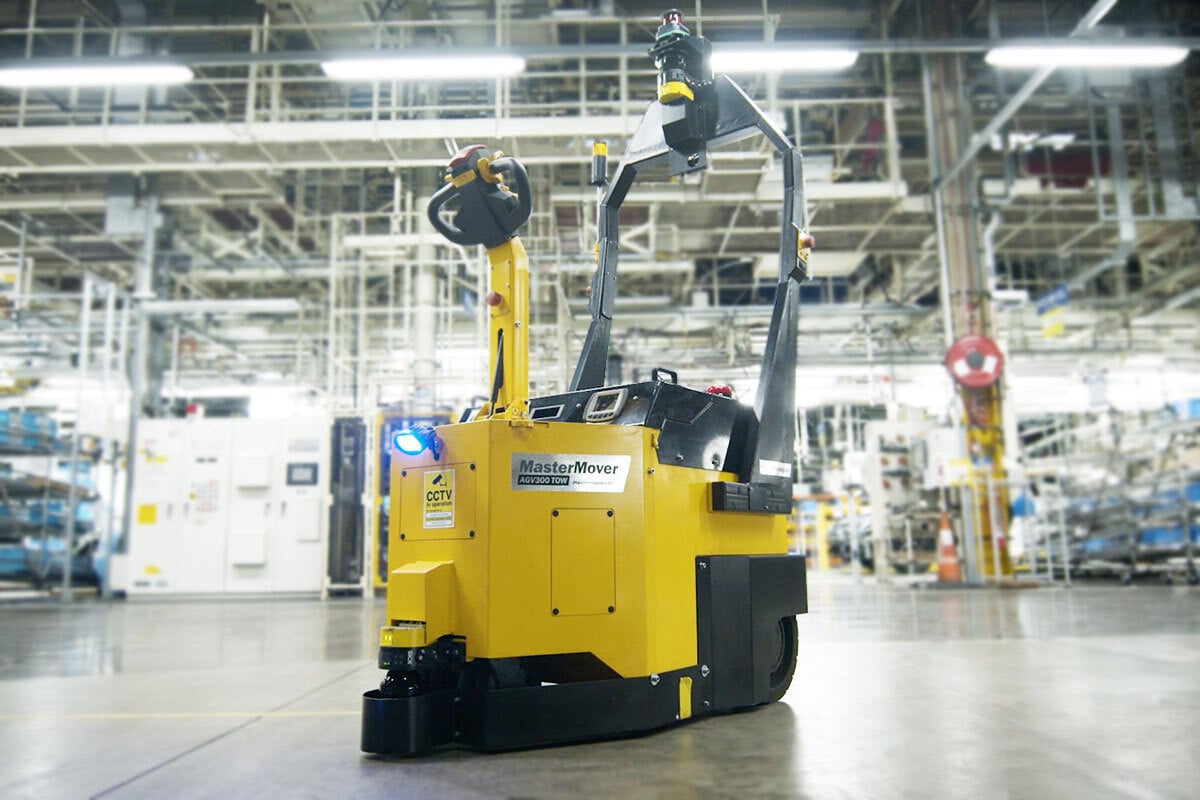
What you need to know
Automated guided vehicles or AGVs, are a type of material handling equipment that moves autonomously – without the need for an operator.
The benefits of scalability and increased efficiency make AGV systems an attractive option for industrial manufacturing settings. With an array of navigational systems available such as scanners, sensors, and line followers – the market for automated guided vehicles of all shapes and sizes has never been stronger.
Despite increasing interest in AGVs, several misconceptions about the functionalities and design exist, from the ease of implementation to perceived cost and return on investment.
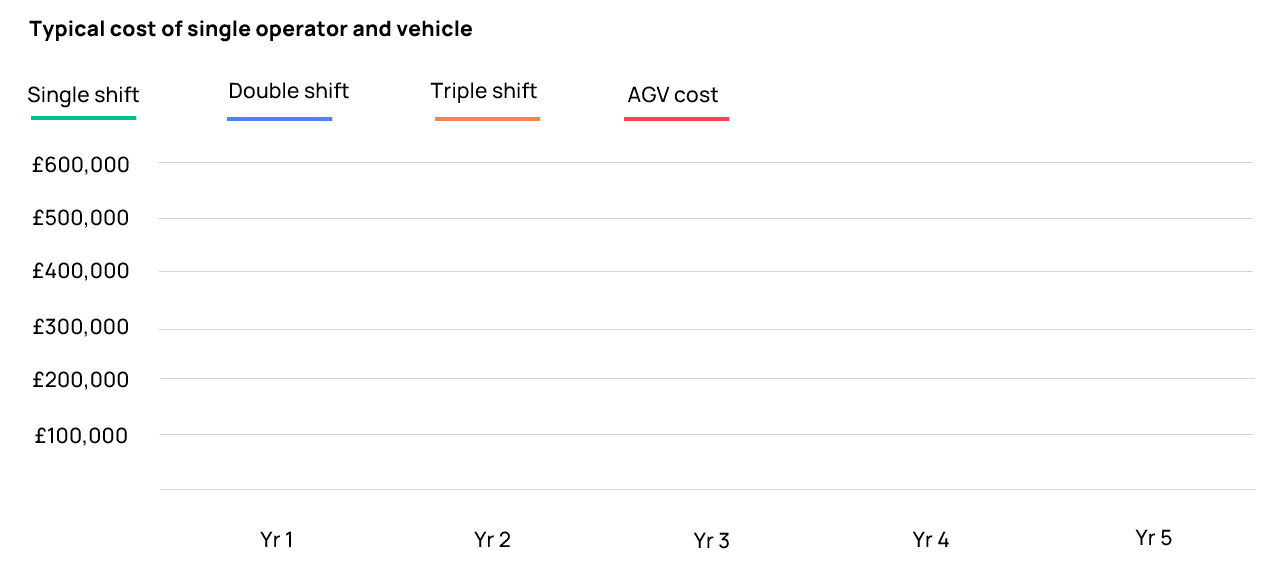
1. Purchase cost & ROI
“An AGV system is too expensive”
Like any equipment, AGVs are an investment and, considering the technology involved they are more costly than their pedestrian alternatives.
Many people perceive AGVs as a high-cost investment with a difficult-to-measure return on investment. An AGV system may feel like a significant upfront investment, but they generally deliver a more substantial return than traditional handling systems. A 24/7 autonomous operation enables you to quickly achieve significant operational cost savings and reduce human error.
It’s worth bearing in mind that the speed at which these returns are seen depends largely on the processes and applications in which the AGV is being implemented. For example, applications requiring frequent movements or previously labour-intensive tasks typically see a quicker return.
Contrasted against fixed automation systems, such as conveyors or crane systems – AGVs offer a more cost-effective, modular solution. Helping to reduce labour costs by increasing efficiency and productivity and freeing up staff to work on tasks delivering a greater value-add.
From a safety perspective, AGVs also reduce accidents and injuries associated with manual handling, reducing the risk of high insurance premiums and costly compensation claims.
For movements requiring the frequent movement of heavy loads along predetermined routes, AGVs deliver an exceptional return on investment. The innate nature of AGV systems means they can operate 24 hours a day, 7 days a week, this continuous operation can typically replace one shift in a traditional transport system.
However, AGVs aren’t for everyone. For applications requiring infrequent movements, transit over relatively short distances or a high degree of positioning, a more operator-involved approach will typically provide a greater return.
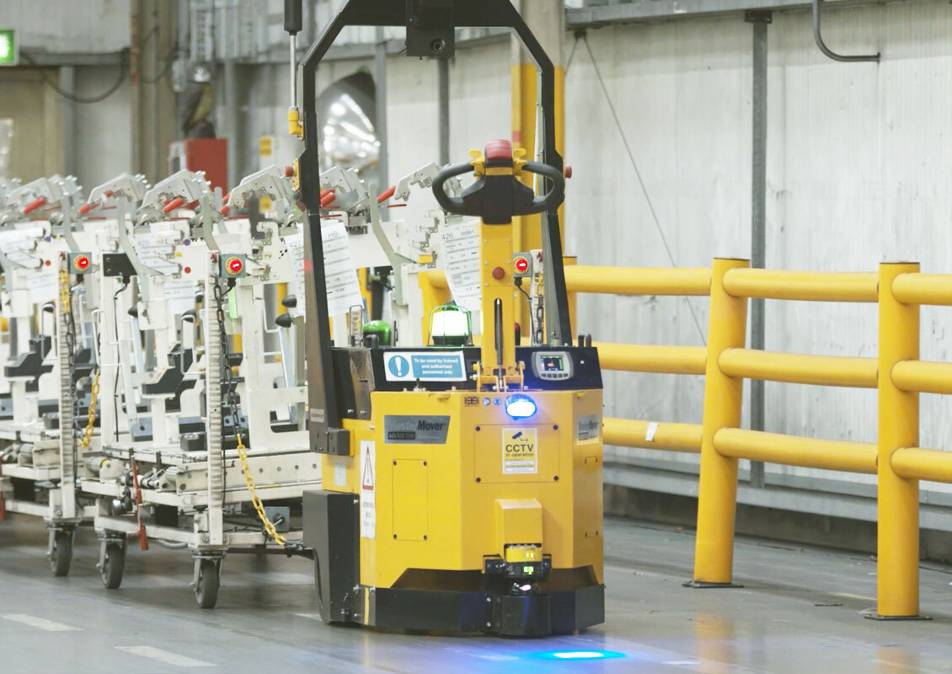
2. Perceived complexity
“Automated guided vehicles are complicated to install and set up”
With the technology available in modern automated guided vehicles, the complexity of installation is a common concern for buyers. Certainly, AGVs are more complex than their operator-driven counterparts, but they are surprisingly easier to implement than you might think.
Understandably, this view of complex installations can deter some companies from investing in the technology. However, with the growth seen in the market, there is continuous innovation to make AGV systems and technology easier to install and more accessible.
The different types of AGVs and their corresponding navigational methods dictate the ease of installation. For example, a line following system, an AGV system in its’ most simplistic form, enables simple cost-effective installation by simply sticking a line of tape that the machine follows. For more complex systems, a reputable supplier will work with you to arrange installation at your site.
Line follow
Set to follow a defined path that can be specified by the operator. Line follow capabilities make sure AGVs follow the same route time after time, even when working in tight spaces or moving loads through areas with minimal clearance.
Barcodes can also be placed on the ground, or other similar identifiable prompts, for the machines to scan for additional programmed information, such as slowing down through a specific area. This makes the environment safer and reduces the risk of damage to high-value loads, the premises, and people.
Natural navigation
The most sophisticated form of AGV, natural navigation machines use sensors and scanning systems to navigate autonomously by detecting and mapping the environment around them to move around obstacles.
The sensors ensure a programmed response to any detected risk and the units will stop until the hazard has been moved away.
In terms of equipment management, AGVs typically feature user-friendly interfaces that make it easy for operators to navigate and monitor the system.
As the name suggests, AGVs operate autonomously, meaning that once set up, AGVs can be left to get on with the task while staff work on other tasks.
8 benefits of AGV systems
Now you understand the differences and types of AGV technology available, the next question you’ve probably got is “What are the benefits of an AGV system?”.
From delivering repeatable movements to increasing safety within congested production environments, AGV systems can provide an array of benefits for industrial manufacturing environments.
-
1. AGVs improve efficiency and throughput
Without the need for an operator, AGV systems dramatically reduce bottlenecks and downtime associated with waiting for licensed drivers or operators.
-
2. They deliver consistent movements
Automated guided vehicles deliver repeatable movements, every time. This delivers safe, precise movements by removing room for human error.
-
3. They reduce labour time
Freeing up employees for value-adding tasks help you make better use of your people and address potential labour shortages.
-
4. They lower costs
They deliver a greater return on investment by optimising people resources and facilitating a 24/7 operation.
AGV systems can also help to reduce accidents and injuries, which can lead to lower insurance premiums and compensation claims.
-
5. They’re flexible and scalable
Can be easily switched to a manual operation mode to move any wheeled load within their weight capability. This enables them to carry out a wider range of tasks, delivering a flexible solution that allows you to scale up or down operations as needed.
-
6. They’re safe
AGVs are equipped with collision avoidance sensors and extensive safety systems to keep people, products, and plant equipment safe.
-
7. They’re customisable
They can be fully customised to fit the specific needs of your processes and operations.
-
8. They’re environmentally friendly
They are emissions-free and help reduce noise pollution and as they’re 100% electric.
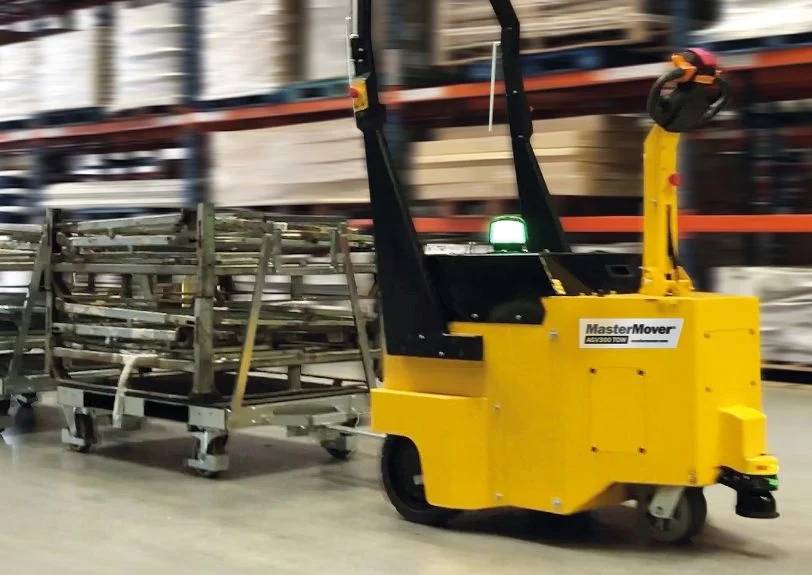
3. Changing production processes
“AGV systems require significant infrastructure changes”
A common misconception shrouding AGVs is the assumption that significant infrastructure changes and modifications are required for the AGV to work.
Yes, AGVs may require you to make some changes or additions to your facilities.
However, these changes are normally minimal, and an experienced supplier will work with you to assess and map out the route the automated guided vehicle needs to run. This considers your existing infrastructure to ensure the AGV can integrate into your existing processes without an overhaul of your current set-up.
For the most common form of AGV system, the extent of infrastructure changes is normally limited to a simple installation of optic tape or paint on the floor – an easy task that enables simple integration.
Other forms of automated guided vehicles such as natural navigational systems utilise sensors and scanning systems to navigate autonomously. In such cases, your supplier will work with you to plan out and conduct any installation required.
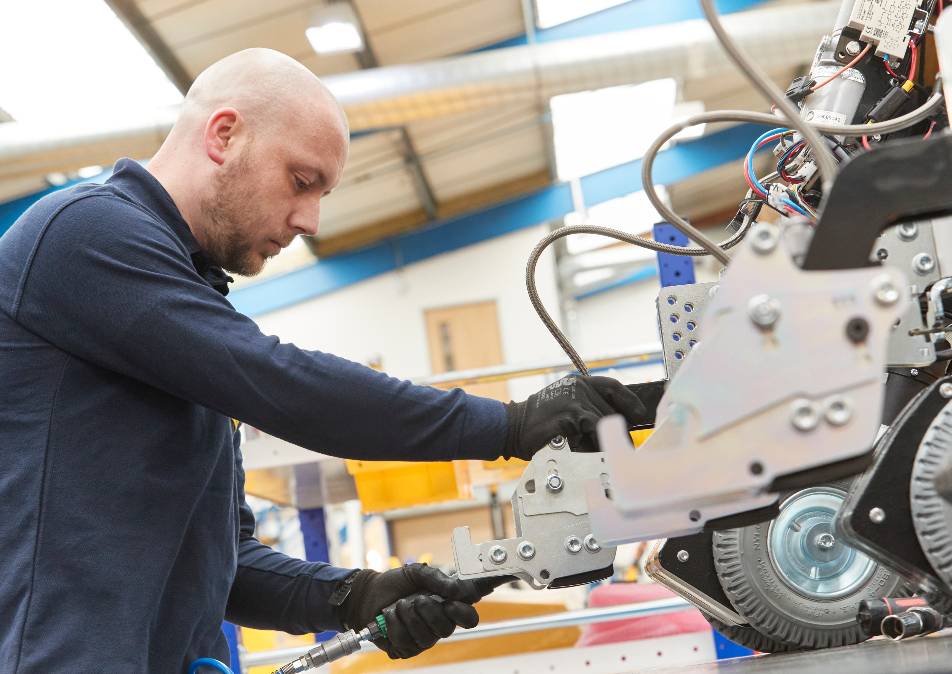
4. Difficult to maintenance
“AGVs are complex – they must be difficult to maintain”
There is a valid perception that an AGV system will be more difficult to maintain and service due to its technical nature. However, AGVs can be easier to maintain as they are less likely to suffer from accidents or damage caused by human misuse or negligence.
The pressures of an industrial environment mean that operators can be hard on aids like material handling equipment. The autonomous nature of an AGV removes the operator involvement and as such, they’re less likely to be knocked around or misused.
AGV systems typically come with support packages that include regular maintenance visits, software updates, and ongoing customer support. This helps to ensure that AGVs are always operating at optimum performance and ensures the longevity of the equipment.
Staff training is also provided. Unlike other types of material handling solutions like forklifts, AGV electric tugs do not require licenses to drive. A short training session is usually enough to educate operators on how to safely utilise the machines, and refresher courses are also available to ensure staff are up to date on the latest technologies and policies.
Getting started with AGVs
Automated guided vehicles offer a versatile and cost-effective way to implement automation and Industry 4.0 technology into your operations. With 24/7 operation, AGVs guarantee high efficiency, reduced downtime, and an excellent return on investment.
MasterMover offers a range of AGV solutions that can be tailored to your specific needs. We also provide ongoing support and maintenance to ensure that your AGVs are always running smoothly.
As an AGV supplier, we’ll help you overcome any perceived barriers and implement AGVs into your workplace with minimal disruption – ensuring a solution that’s ready to get to work for you.
The ultimate guide to AGV electric tugs
Automated Guided Vehicles (AGV)
Looking to understand AGV systems in a little more detail?
We’ve compiled some helpful resources to get you started, covering everything you need to know.