Managing Safe Material Handling in Pharmaceutical Manufacturing
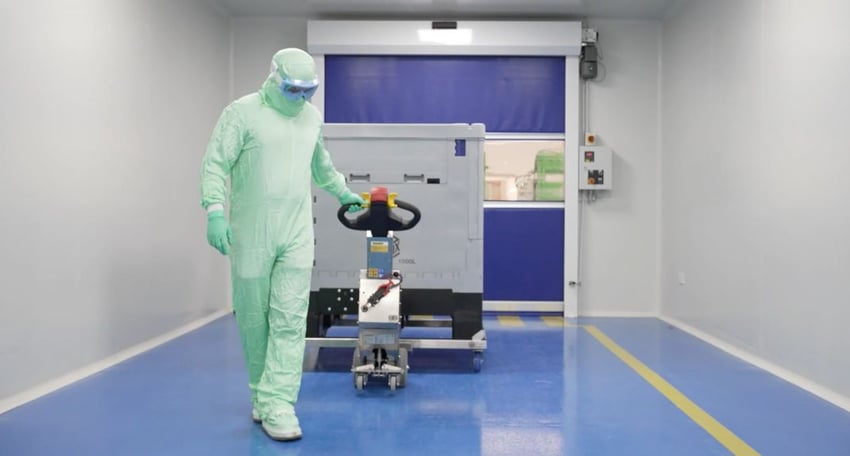
The pharmaceutical industry places a high importance on safety, and this includes the handling of materials. Within pharmaceutical manufacturing, it is crucial to have systems and procedures in place to ensure that materials and equipment are handled safely.
There are a number of key considerations when it comes to managing safe material handling in pharmaceutical manufacturing:
- Ensuring that all raw materials and finished products are properly labelled and stored
- Having proper ventilation and lighting in storage and manufacturing areas
- Regular cleaning and maintenance of storage and manufacturing areas
- Providing training to employees on safe material handling procedures
- Using the correct equipment and technology for material movement
By following these key considerations, pharmaceutical manufacturers can help to ensure the safe handling of materials and equipment in their facilities.
Let’s take a look at each more in-depth.
1. Ensuring Materials Are Labelled & Stored Correctly
One of the key ways to ensure the safe treatment of materials is by ensuring that all materials are properly labelled and stored. This means that employees will know exactly what they are handling and where it needs to go – particularly important when dealing with large scale production, where things can easily get lost or confused.
Labels should be clear and easy to read and should include information such as the name of the material, its strength and dosage, the batch number, the expiration date and any special handling instructions. A system for traceability should also be established so every batch of product can be traced back to its raw materials.
It is also important to store materials in the correct areas according to their hazard class. For example, flammable materials should be stored away from ignition sources, and corrosive materials should be stored away from food products.
Similarly, any equipment being used to move hazardous or precious loads need to be up to the job; fuel-powered machines are a huge safety risk in flammable environments and the correct steps need to be taken to minimise the risk of injury, damage to goods and downtime due to lost or damaged materials and infrastructure.
2. Having Proper Ventilation and Lighting
Safely storing hazardous materials requires careful attention to ventilation and lighting. Adequate ventilation helps to prevent the accumulation of harmful vapours, while proper lighting minimises the chance of accidents. Employees should be aware of the location of emergency exits and fire extinguishers and should know how to safely handle hazardous materials. By taking these precautions, employers can help to create more secure manufacturing processes and a safer working environment.
3. Cleaning & Maintenance of Storage and Manufacturing Areas
Regular cleaning and maintenance of areas is crucial in ensuring the safe manufacture and handling of materials. Storage and manufacturing areas should be kept clean and free of debris and should be well-maintained with the proper components in place, so that any potential hazards are identified and addressed quickly.
4. Providing Training to Employees On Safe Material Handling Procedures
It is essential that employees are properly trained on how to handle materials safely. This includes understanding the hazards associated with each material and knowing the correct procedures and processes for handling them safely.
Employees should also be trained in how to use the equipment properly, so that there is minimal risk of injury when moving materials around the facility. Refresher courses should be regularly undertaken to ensure staff are up to date on the latest policies, and machines should be serviced regularly. This also reduces the risk of damage to loads and surrounding factory infrastructure.
5. Using the Correct Equipment for Material Movement
Pharmaceutical manufacturing typically takes place in cleanroom environments, and often a more manual handling approach is used. However, this increases risk to both employees and the materials being moved and takes people away from tasks of higher value.
Due to their nature, cleanroom environments are usually tight spaces so, combined with the movement of high value equipment and hazardous materials, it’s essential that the correct type of equipment is available and used.
The production of pharmaceutical products requires several intermediate processes to create the finished item, and each process requires safe and careful handling.
Electric tugs are ideal for moving fragile loads in manufacturing processes, particularly in pharmaceuticals, due to their ease of use and the high degree of control and manoeuvrability they offer.
Electric tugs are designed to start and stop the movement of loads in a controlled manner. In addition, electric tugs are easy to operate, which means that employees can be trained quickly to use them safely. There is no need for a license and a simple instruction will allow any staff members the ability to operate them.
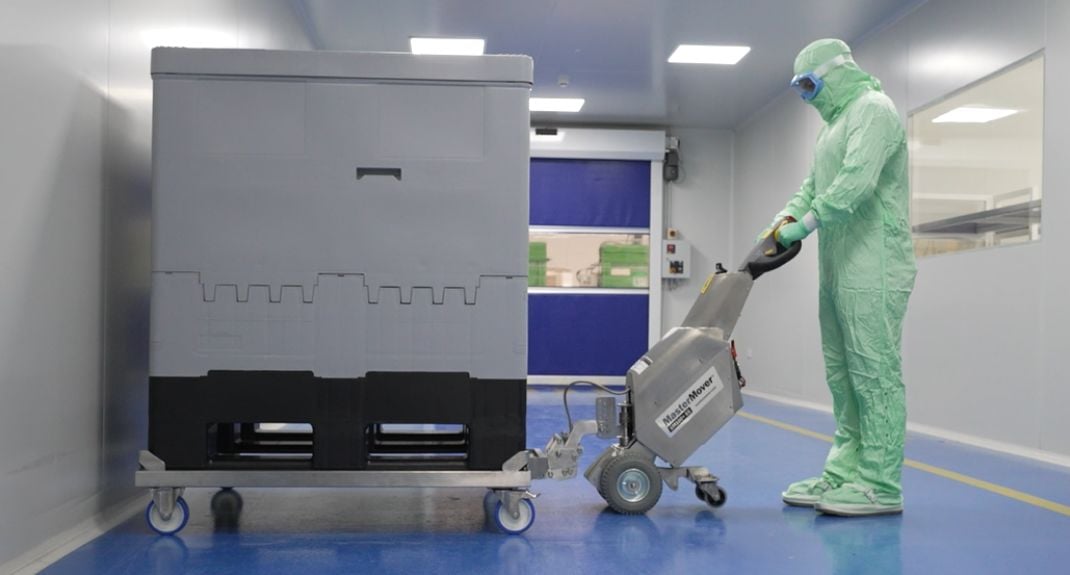
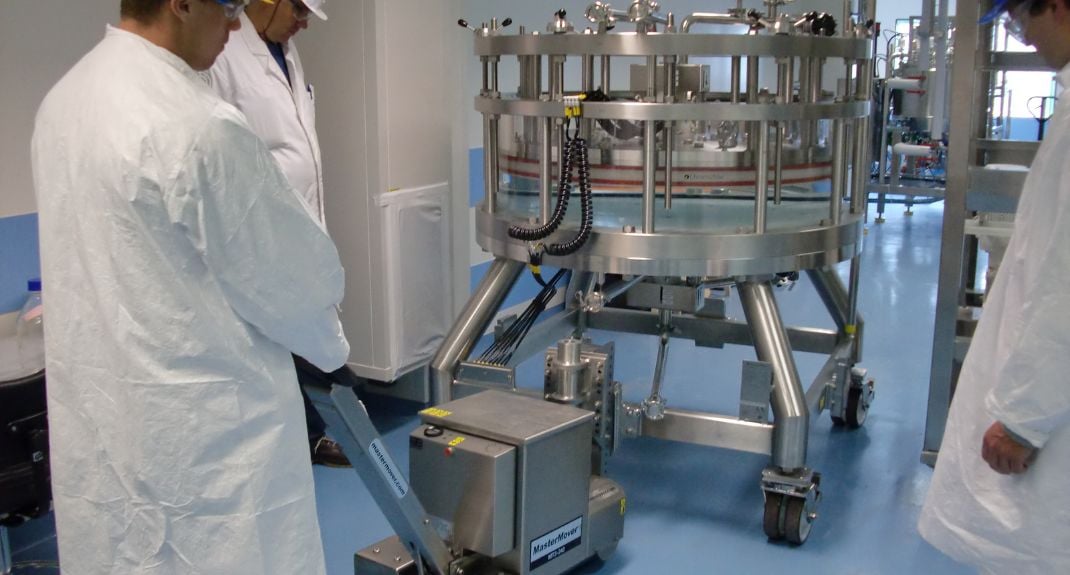
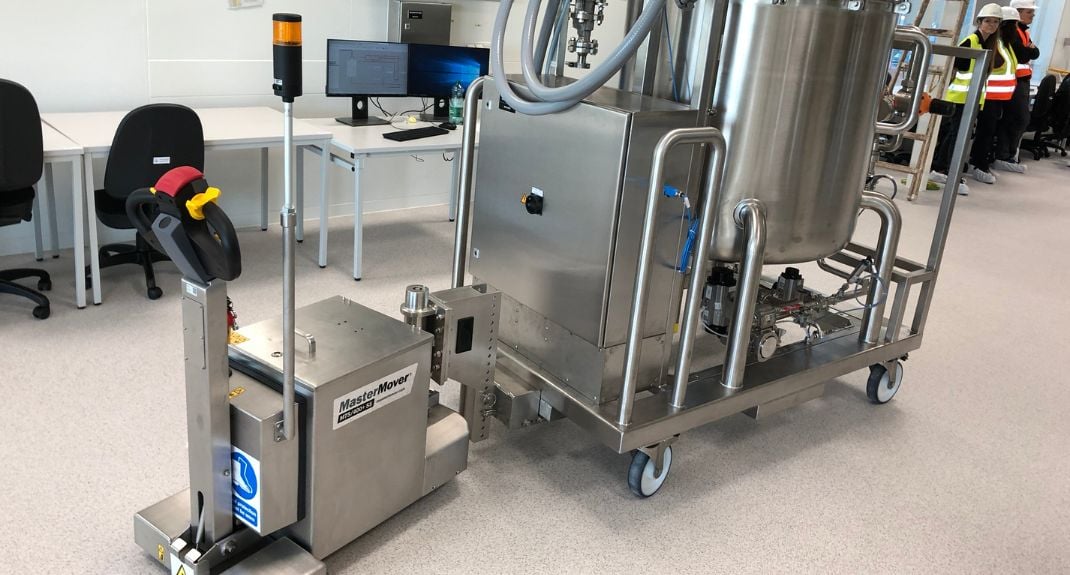
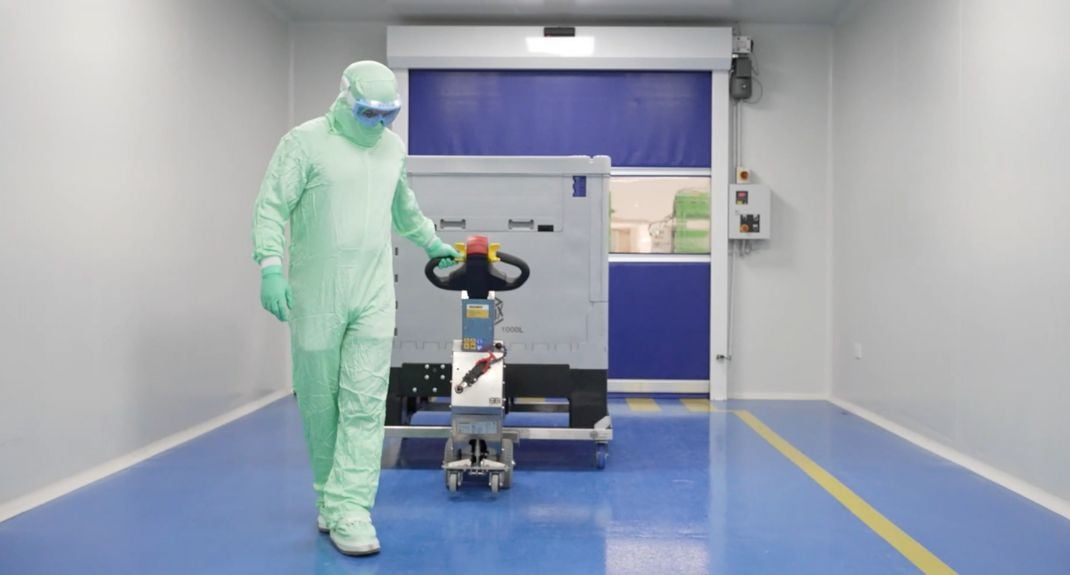
Selecting the Best Materials for Pharma
In the pharmaceutical industry, cleanliness is paramount. This is to help safeguard the manufacturing process when the mass production of pharma products is undertaken. Any contaminants, such as dust or bacteria, can jeopardize the safety of products and lead to costly recalls.
That’s why stainless steel is a high-demand material in the pharma industry. Not only is it easy to clean, but it also resists corrosion and stands up to repeated cleaning cycles. As a result, stainless steel is the material of choice for many pharma companies when it comes to their electric tugs.
The stainless-steel electric tug – designed for use in cleanroom environments – means that it can be easily cleaned and sterilised, helping to ensure the safety of drugs and clean rooms and protecting against costly recalls.
Why Electric Tugs Are the Equipment of Choice in Pharmaceutical Manufacturing
Electric tugs are an ideal choice for moving materials in a pharma manufacturing facility. Electric tugs do not release any harmful gases, fumes, odours, or other emissions into the atmosphere, making them an environmentally friendly option. They are also quieter than other load movement solutions, meaning they have been developed to create less noise pollution.
They are also reliable, easy to service and require little maintenance, therefore helping to reduce overall costs over time.
Finally, they are highly flexible, able to move a range of items as required. And should the layout of a facility, or processes, change, the electric tug continues to work seamlessly within the operation.
Managing Safe Material Handling in the Pharmaceutical Industry with MasterMover
Managing safe material handling in pharmaceutical manufacturing is vital for the safety and welfare of your staff, as well as the protection of key infrastructure and products. The best way to ensure compliance with cGMPs (Current Good Manufacturing Practices) and other regulations is to invest in high-quality equipment that meets or exceeds industry standards.
If you’re interested in discovering the best material handling solutions in pharmaceutical manufacturing, contact us today. We supply top-of-the-line products and services that are designed to meet the unique needs of our clients. With our help and expertise, you can transform your manufacturing methods and rest assured knowing that your facility is compliant with all applicable regulations.