電動拖車 – 搬運產品、設備和物料的更佳方式
利用電動拖車,一名操作員能夠搬運重達 70,000 公斤或以上的輪式荷載。憑藉全方位產品系列(包括步行操作式電動拖車、遙距控制和自主 AGV 系統),您可利用 MasterMover 電動拖車,達至更安全的操作流程,同時提高效率。
多年經驗
25 年來,我們致力於提供有效的物料搬運解決方案。
國家
我們的機器被世界各地的客戶使用。
機器交付
我們的電動拖船和拖車日復一日地使用,以提供安全、高效的負載移動。
小巧強大的電動拖車解決方案
我們由電池驅動的電動拖車和拖輪車經精心設計,遵循相同的指導原則 – 無論您要搬運 500 公斤或 70,000 多公斤,都可獲享可靠性能。
電動拖車(按系列分類)
SmartMover
2,000 公斤
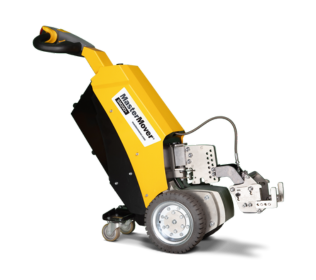
SmartMover 小巧而強大,是理想的人手搬運解決方案,在提高工業製造、零售和 物流領域安全性方面,深受信賴。
MasterTow
20,000 公斤
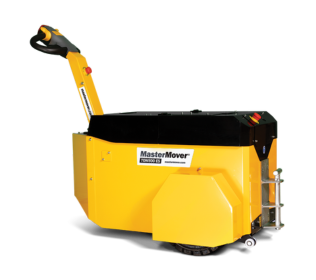
利用我們的專為安全搬運重達 20,000 公斤荷載而設計的強大電動拖車,提升安全性與效率。
MasterTug
20,000 公斤

利用 MasterTug 系列,單名操作員可透過步行操作方式,輕鬆推動、拉動及轉向重達 20,000 公斤的重型荷載。
MasterHandler
4,000 公斤

利用 MasterTug 系列,單名操作員可透過步行操作方式,輕鬆推動、拉動及轉向重達 20,000 公斤的重型荷載。
AllTerrain
5,000 公斤
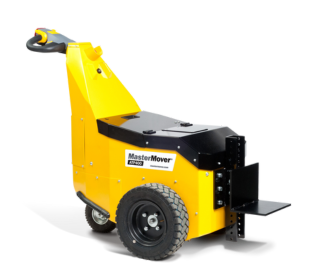
在嚴苛的環境條件下呈獻強大性能,選用 AllTerrain 系列,在腳輪和滑軌上安全搬運重型荷載。
Trailer Moving System
20,000 公斤
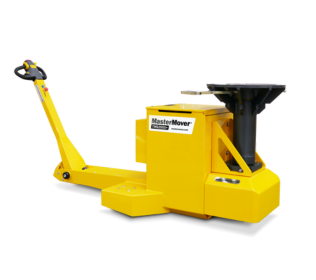
要在製造和營運場地中搬運重達 20,000 公斤的空載拖車,Trailer Moving System 是理想的解決方案。
PowerSteered
70,000 公斤
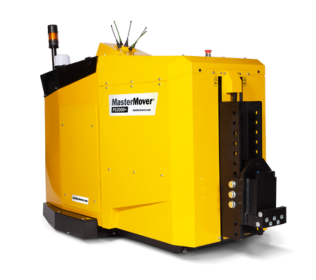
專為最高能見度而設的遙距控制解決方案,可搬運重達 70,000 公斤的荷載;配合我們的專利 MultiLink 解決方案,可征服更重型的荷載。
不銹鋼
15,000 公斤
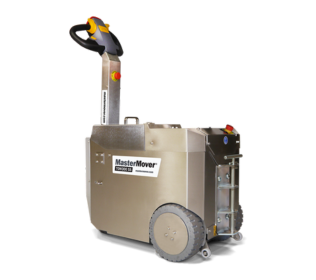
不銹鋼電動拖車以高級 316 不銹鋼製成,備有高達 IP55 的防護等級,因而完美符合食品和製藥環境的嚴格要求。
行業專用解決方案
電動拖車可提高工作場所的安全性,同時提升各行各業的營運效率。無論是要搬運零售業的籠車、航空航天製造領域的複合物料,甚至是風機渦輪葉片,都可確保安全無虞。
航空航天
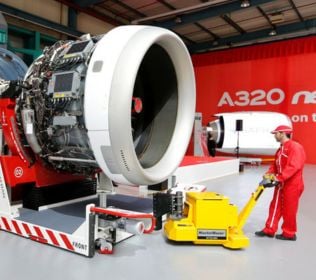
利用電動拖車,在航空航天業中實踐更安全的物料搬運流程。
能源和石油化工
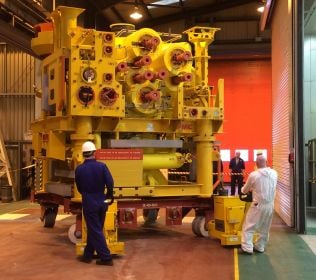
全面提高能源業重型荷載的性能和操控性。
汽車業和重型工廠
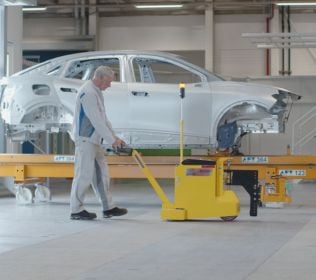
選用電動拖車,提升精益流程,同時提高廠房靈活性。
食品及飲品
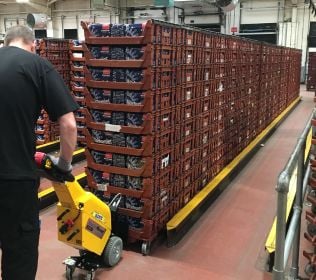
利用電動拖車省卻人手搬運,令食材搬運更安全,大幅提高效率,同時減低受傷風險。
零售、物流和倉務
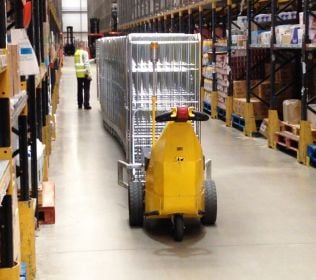
理想的人手搬運解決方案,大幅提高零售和物流領域的效率與安全性。
製藥和生命科學
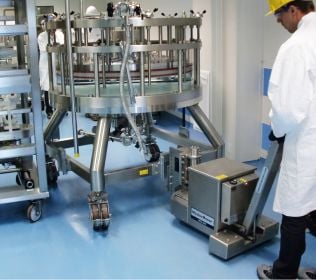
安全操控高價值的重型設備,省卻人手搬運,並大幅提高生產效率。
設施和廢料
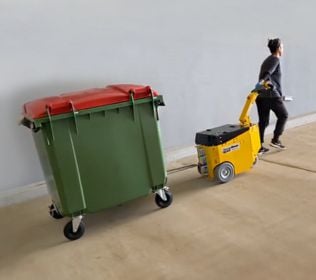
省卻人手搬運,並大幅提高設施和廢料管理領域的安全性。
製造和裝配
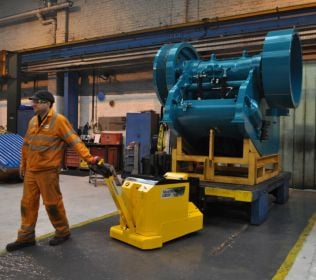
工業製造商信賴電動拖車,以提升工作場所的安全性,同時提高營運效率。
當然,我很樂意向其他有意實踐自動化駕駛流程的組織推薦 MasterMover AGV。
Kevin Jones豐田汽車
我們能夠在許多場地部署電動拖車,而用戶也提供了非常正面的評價。
Joel OddouxSicarev
它們品質優良,專業可靠,且易於操作。此外,它們更可在狹小空間內帶來出色的控制性與搬運效能,十分適合用於生物製藥業
John O'ReillyStrikebox Engineering
SmartMover 電動拖車完美切合我們的需求,尤其在斜坡上下搬運的場景。
Jim FrielFriel Enterprises
這些拖車讓我們能夠改變生產方式,提高廠房效率,打造更安全的環境。
Steve GriffithsSelect Plant Hire