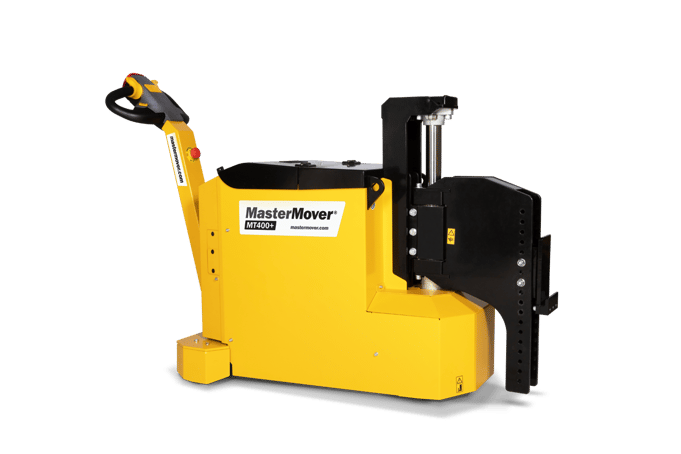
MasterMover Blog
Benvenuto nel blog MasterMover, il tuo hub per le ultime competenze, approfondimenti sul settore e risorse essenziali per ottimizzare i processi di movimentazione dei materiali.
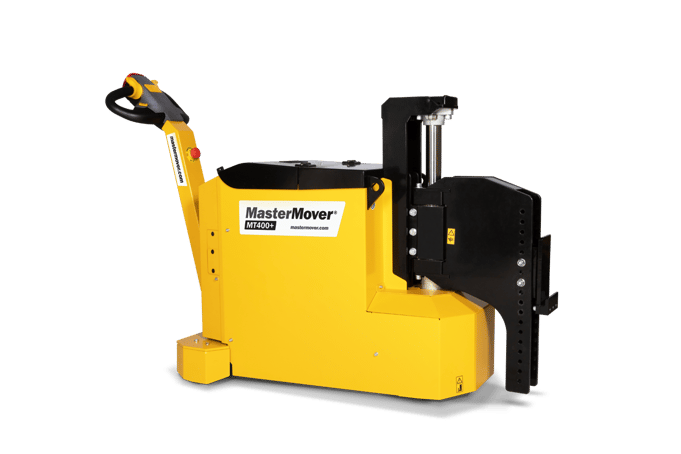
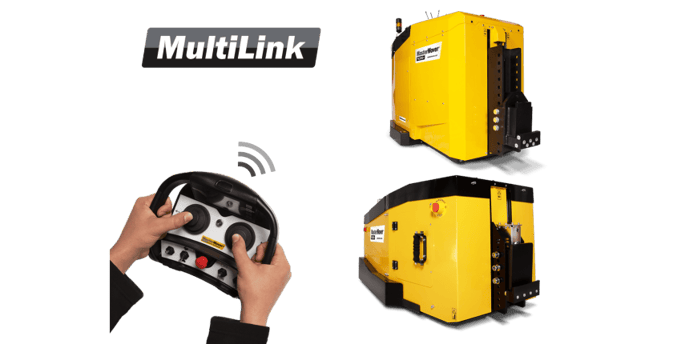
Cos’é la tecnologia ‘MultiLink’ di MasterMover?
La nostra tecnologia MultiLink è una comunicazione wireless che permette di collegare insieme due o più movimentatori elettrici in modo che possano lavorare in sincronia per rendere semplice la movimentazione di carichi lunghi, scomodi o pesanti.
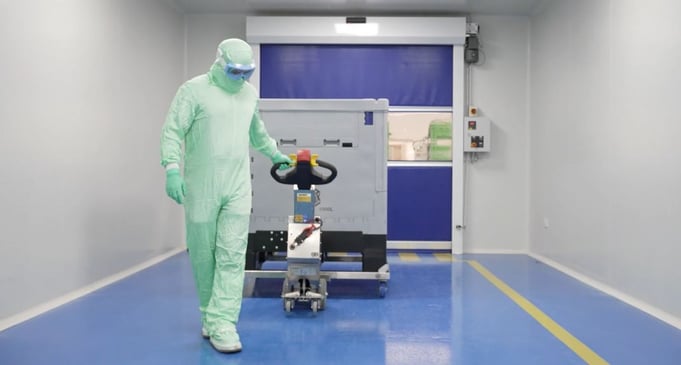
Come rendere sicuro il material handling nell’industria farmaceutica
L’industria farmaceutica attribuisce grande importanza alla sicurezza, e ció comprende anche la movimentazione. Infatti è fondamentale disporre di sistemi e procedure che garantiscano che i materiali e le attrezzature siano manovrati in modo sicuro.
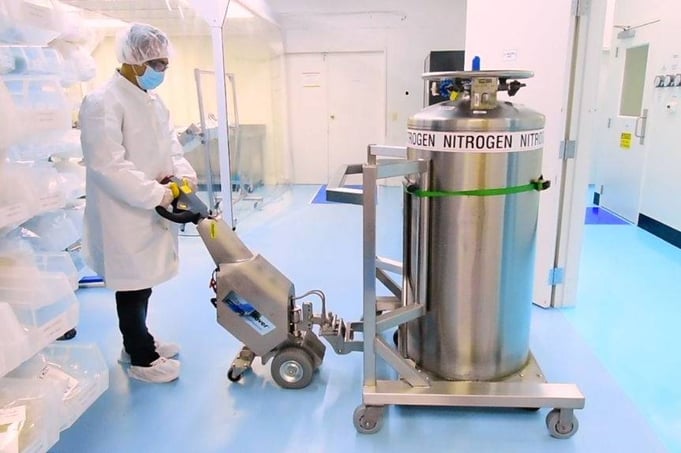
8 Sfide del material handling negli impianti farmaceutici
La produzione di prodotti biofarmaceutici è un processo complesso. Oltre alle sfide che la maggior parte dei produttori si trova ad affrontare, le società biofarmaceutiche devono lavorare nelle camere bianche, che sono aree chiuse in cui la ...
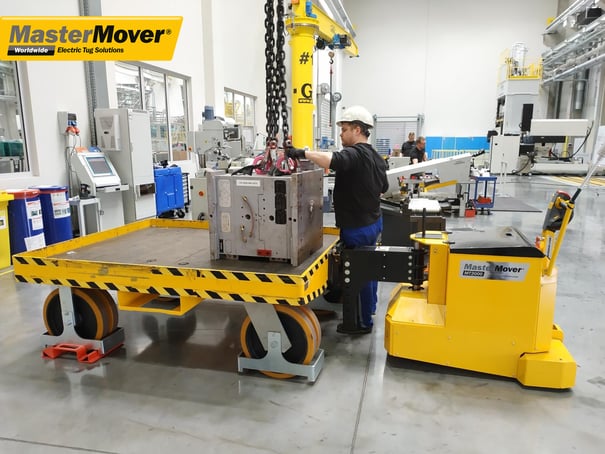
Un modo più sicuro di movimentare gli stampi a iniezione
La movimentazione di pesanti stampi a iniezione rappresenta una necessità abituale per i fornitori automobilistici di tutto il mondo. Gli impianti di produzione utilizzano solitamente una serie di carri ponte per trasportare gli stampi, ma ...
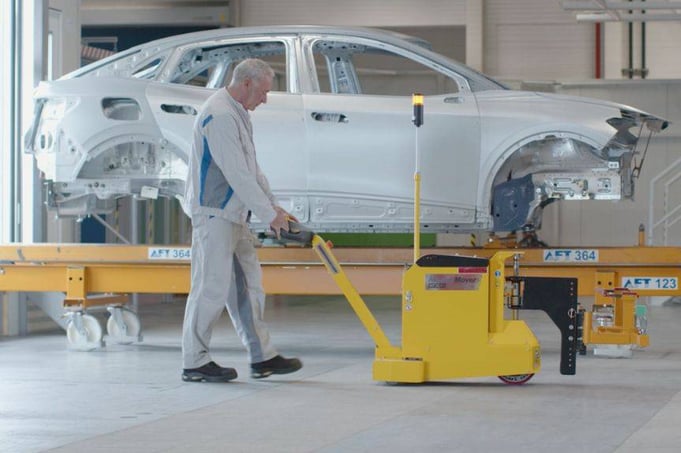
Soluzione MasterTug utilizzata da produttori automobilistici di fascia alta per movimentare attrezzi compositi
Vari produttori di auto sportive di fascia alta utilizzano i trainatori elettrici MasterMover per movimentare utensili compositi pesanti e componenti di grandi dimensioni come i telai.
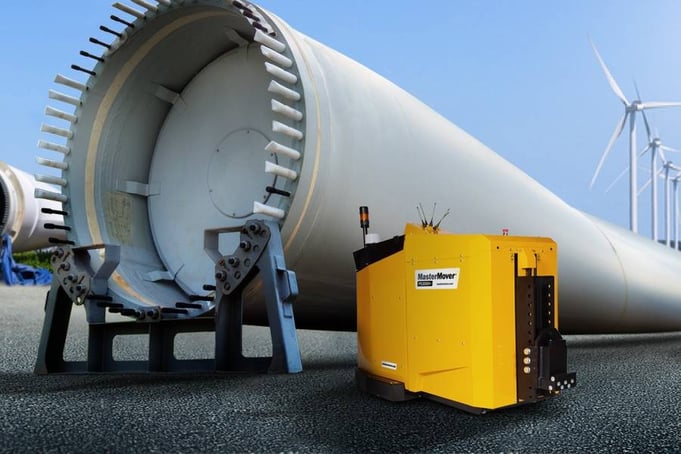
Movimentare pale eoliche durante la produzione: ecco la soluzione
Movimentare le pale delle turbine eoliche durante la produzione può rappresentare una sfida, infatti possono raggiungere i 100m di lunghezza (la piú grande al mondo misura 107m) e pesare molte tonnellate. É qui che i movimentatori elettrici ...
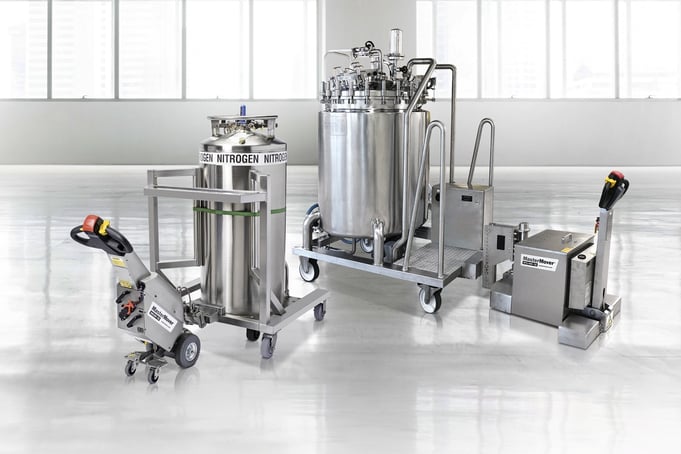
Il ballroom non dovrebbe essere estenuante
Il concetto “ballroom” visualizza “la fabbrica del futuro” degli stabilimenti produttivi farmaceutici. Questa evoluzione, però, crea anche lei nuovi rischi di sicurezza per i lavoratori?
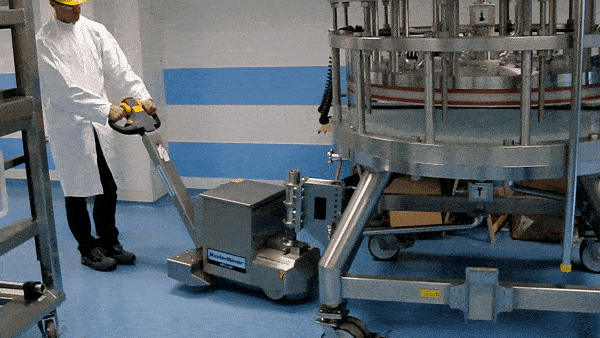
Come ottenere una gestione sicura delle colonne per cromatografia nella camera bianca
I grandi nomi dell’industria farmaceutica utilizzano i trainatori elettrici di MasterMover per spostare le colonne di cromatografia, grazie alla loro combinazione ottimale di movimentazione di carichi pesanti, dimensioni compatte, manovrabilità ...